Chassis Systems ─ Heading Toward Steer-By-Wire
Clément Feltz | Simon Sagewka | Benjamin Severin | Markus Stiegler
Vehicle automation represents the second major transformation underway in the automotive world. In this context, Schaeffler expects that as early as 2035, every fourth vehicle manufactured will have at least automation level 3 (SAE L3). This, in turn, will bring with it consequences in terms of safety and comfort requirements, but also new opportunities with respect to interior design ─ up to and including all-new vehicle concepts.
In the automotive industry, steer-by-wire is considered a prerequisite for implementing autonomous driving. Schaeffler supports the introduction of this technology by developing innovative components and systems as well as controls for by-wire steering setups on the front and rear axles. The mechatronic rear-axle steering system (iRWS) will go into volume production in 2022. In the case of front-axle steering systems, targeted development is taking a commercial vehicle route (EHPS) and is based on the experience and expertise gained with the Space Drive system from Schaeffler, which is suitable as an add-on concept for steer-by-wire retrofitting of prototypes to small vehicle fleets. The fully integrated front wheel steering system (FWS) focuses on the full replacement of conventional steering systems in volume-based applications. In fully automated vehicles, this design facilitates operating concepts whereby the steering wheel fully retracts into the dashboard during highly automated driving mode to create additional space for the driver.
- Chassis technology roadmap
- Ball screw drive
- Active roll control system
- Mechatronic rear-axle steering system
- Mechatronic power pack for EHPS
- Steer-by-wire solutions
- Space Drive
- Fully integrated by-wire steering system
- Hand wheel actuator
- Electrically adjustable column
- Road wheel actuator
- Summary
- Literature reference
Chassis technology roadmap
For many years now, Schaeffler has been supporting automotive manufacturers in chassis development by supplying individual components such as wheel bearings, strut bearings, spring cup bearings and universal joint bearings. Building on this, Schaeffler has defined a technology roadmap for chassis development activities moving toward ever more complex systems (Figure 1). Starting with high-precision mechanical components, this roadmap extends from mechatronics to steer-by-wire systems and culminates in fully integrated rolling chassis concepts.
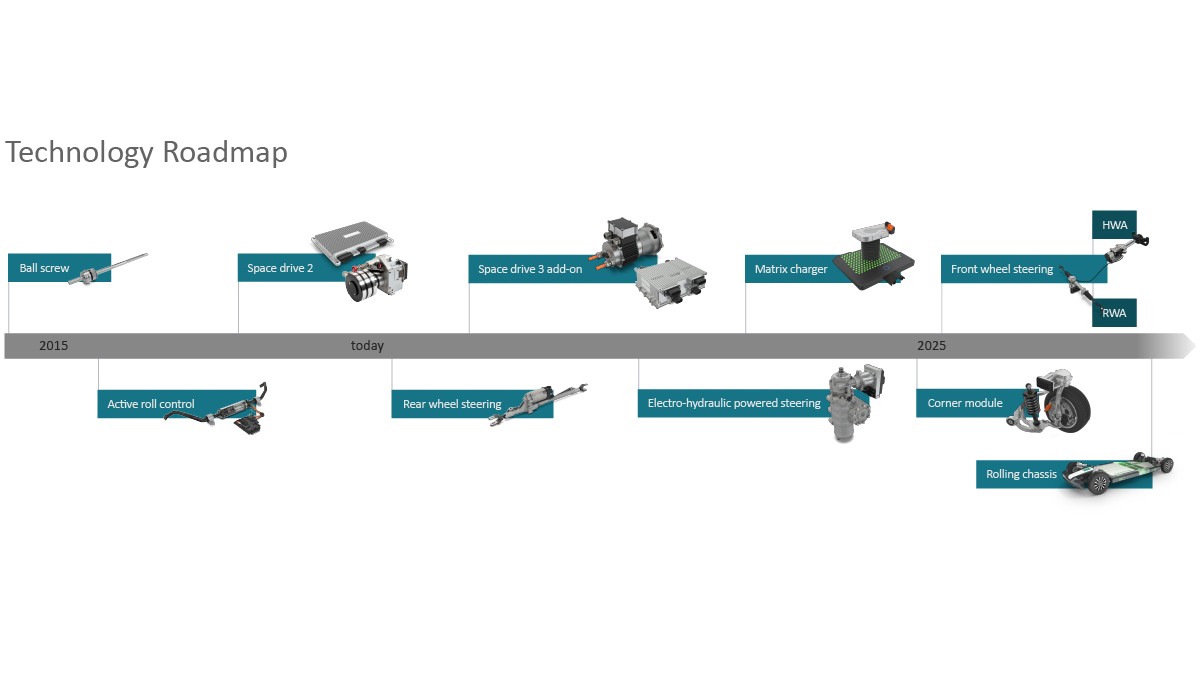
The products that play a key role in developing by-wire systems are discussed in greater detail below as examples of Schaeffler’s core competencies and future chassis development activities. The development and design of the corner module, rolling chassis and matrix charging system are highlighted in another technical article that can be found in [1].
Ball screw drive
The first product on the chassis technology roadmap is the ball screw drive, which is rooted in machine tool building technologies and was introduced in 2009. It is employed in numerous chassis systems, such as in electromechanical steering systems or brakes. The high-precision mechanics implemented underlines one of Schaeffler’s core competencies by offering significant benefits when it comes to developing other products in the chassis portfolio. As a replacement for conventional hydraulic power steering systems, the ball screw drive provides better comfort and lower fuel consumption in a direct comparison. The integrated four-point bearing also helps the available installation space to be optimized (Figure 2).
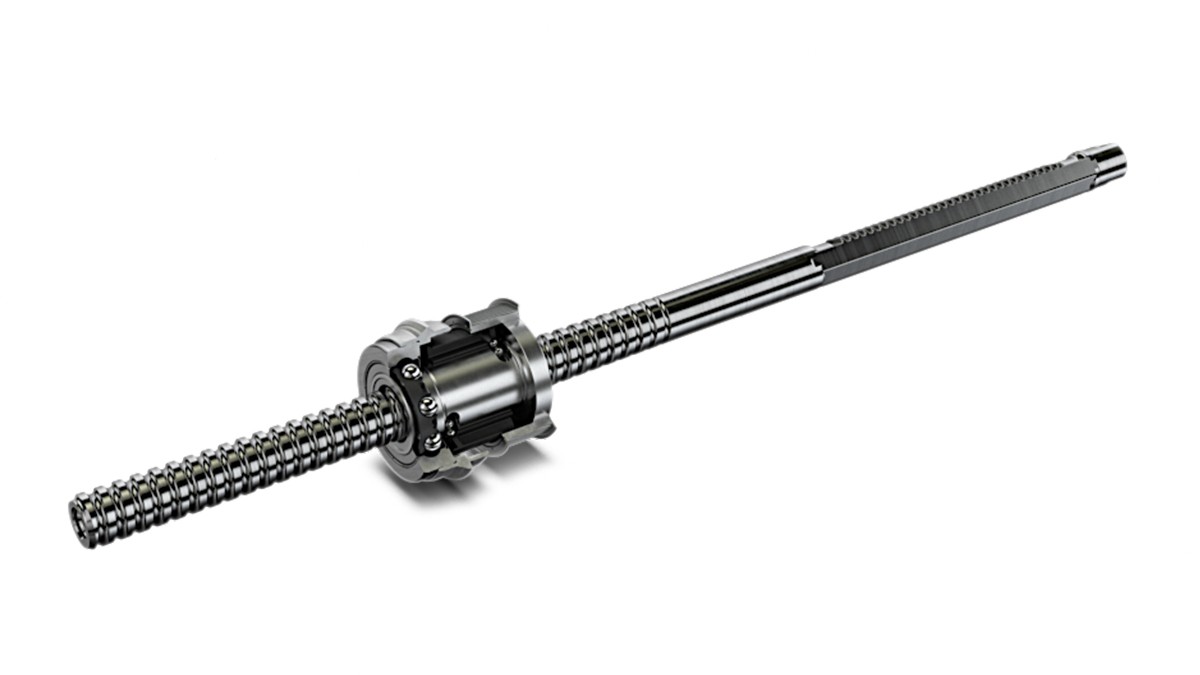
Active roll control system
The mechatronic active roll stabilizer from Schaeffler entered volume production back in 2015 (Figure 3). In so doing, it became the first chassis actuator worldwide to be manufactured on a mass scale as a 48 V variant. For its development, Schaeffler was presented with the 2016 German Innovation Award in the large-scale enterprise category, among other distinctions. Compared to passive stabilizers, the active solution from Schaeffler offers a significantly better perception of vehicle stability thanks to a reduced roll angle. Improved driving dynamics and safety as well as better ride comfort are also achieved.
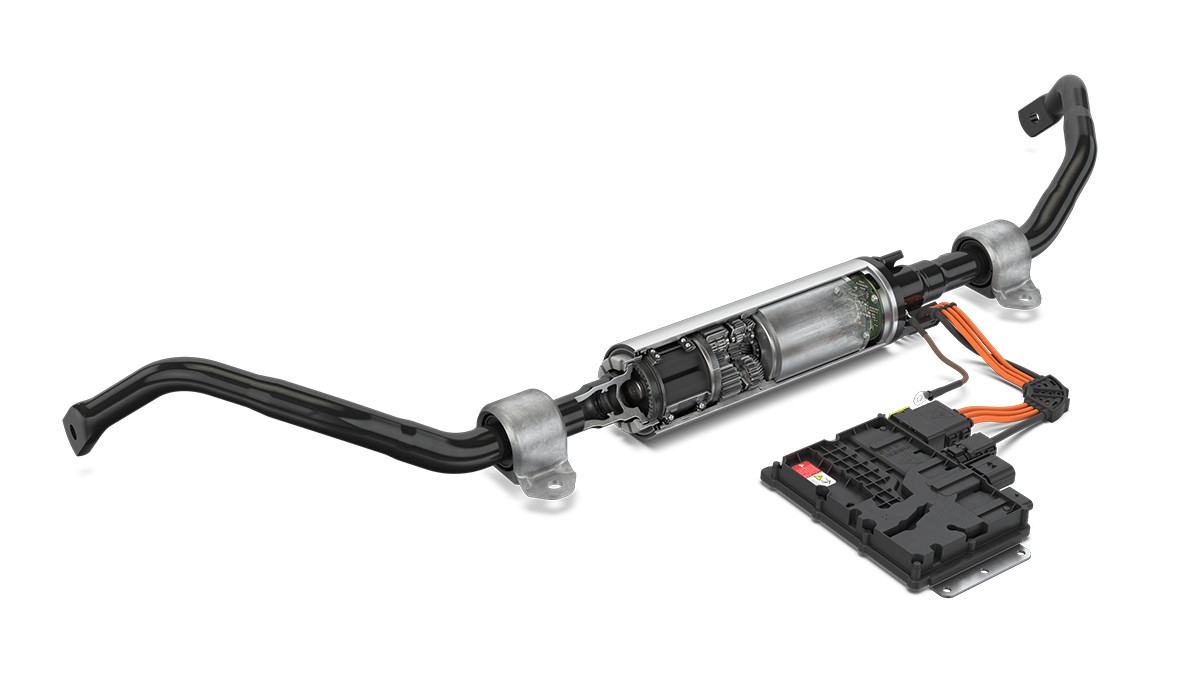
Mechatronic rear-axle steering system
Echoing the increasing demand for battery-electric vehicles with an extended range are batteries with ever greater capacity installed in vehicle underbodies. This equates to a longer wheelbase as compared to vehicles with an internal combustion engine which, in turn, reduces the overall maneuverability (= larger turning circle) of the vehicle. When maneuvering, rear-axle steering reduces the turning circle and increases maneuverability by steering in the direction opposite to the front wheels [2]. At higher speeds, it further optimizes handling by allowing the rear axle to turn in the same direction as the front axle, thereby improving vehicle stability and ride comfort as well as enhancing vehicle safety. It also improves the active intervention possibilities of automated lane change assist systems.
In developing the rear-axle steering system, Schaeffler leveraged its strengths and core competencies as well as the experience it has gained with mechatronic systems. The mechatronic rear-axle steering system (iRWS) (Figure 4) allows the company to offer a complete system, thereby taking the first step toward becoming a steering system supplier.
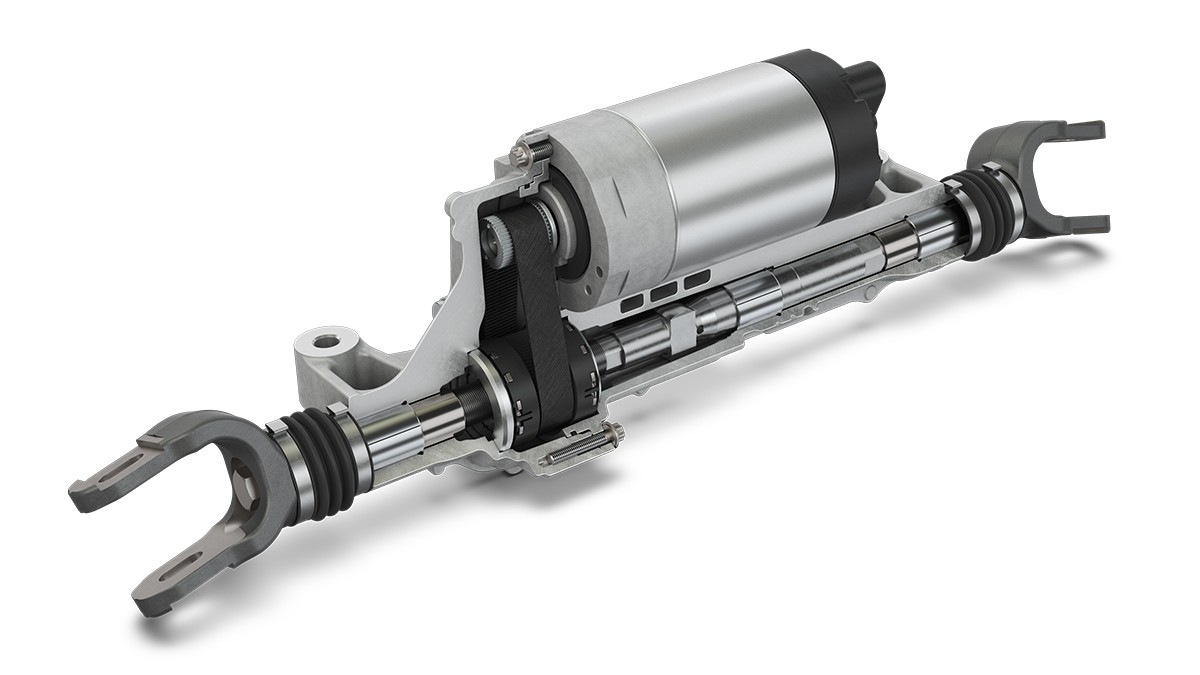
The iRWS comprises two subsystems: the mechanical system with a planetary roller gear (PRG) forming the basis and the power pack, which houses the electronics, electric motor and software. To this end, Schaeffler is responsible for the entire system as well as integrates it into the vehicle.
The rear-axle steering system is developed in line with the requirements of Automotive Safety Integrity Level (ASIL) D, which places high demands on system safety. In the event of a functional failure of the rear-axle steering system, for example, uncontrollable steering movements of the rear axle must not occur under any circumstances. Instead, the rear-axle steering system must self-lock and “freeze” the last steering angle set. To meet these safety requirements for the system, Schaeffler decided in favor of a planetary roller gear (PRG) (Figure 5). The advantage of the PRG as compared to the trapezoidal lead screw drives frequently used by competitors is the combination of high efficiency with a self-locking function.
Figure 6 graphically illustrates the relationship between efficiency and force. The self-locking limit is indicated by the dotted red line. Trapezoidal lead screw drives (gray curve) achieve significantly lower efficiencies, but are in turn inherently self-locking. With planetary roller gear, the efficiency and locking characteristics heavily depend on the preload force of the planets and support bearings. Without self-locking, they achieve efficiencies in the region of 80 percent (light green curve). The Schaeffler design for the iRWS (dark green curve) offers the best possible compromise between good efficiency and self-locking force by applying targeted preloads using high-precision bearing technology.
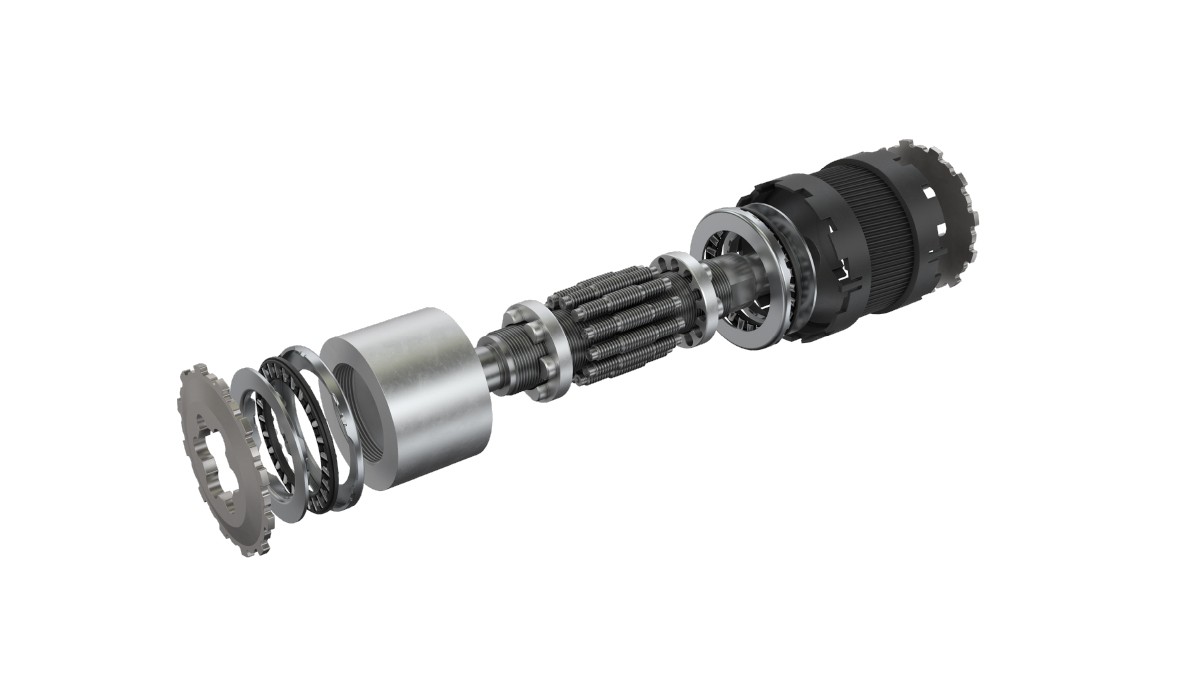
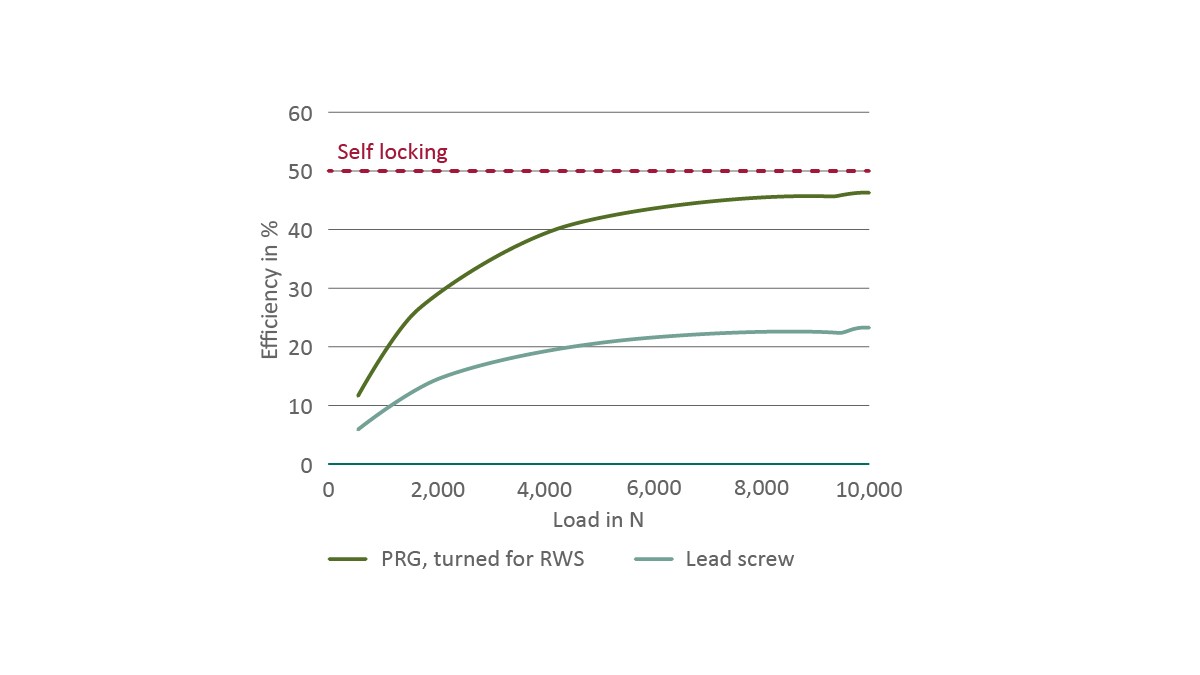
The power pack comprises an electric motor and the drive electronics. The software integrated in the electronics can be subdivided into basic and application software. Schaeffler utilized the knowledge gained from previous projects such as active roll stabilization to develop the application software in house. This includes the module for adjusting the required rear-axle steering angle. Some projects also involved integrating vehicle control scopes, whereby the target rear-axle steering angle ideal for the driving situation is calculated based on select vehicle parameters.
Mechatronic power pack for EHPS
The electrohydraulic steering system (EHPS) is specially designed to steer the front axle of commercial vehicles. It comprises a hydraulic unit and a power pack. Schaeffler assumed development of the power pack (Figure 7) and overall system integration, marking the next step for Schaeffler as a supplier of front-axle steering systems. The EHPS is set to launch in 2023.
The EHPS power pack is developed as a “fail-operational” system in line with ASIL D requirements. It facilitates electronic intervention in the steering system by producing an additional steering torque on the power steering components. This improves driving safety and comfort as well as enables automated driving functions to be integrated.
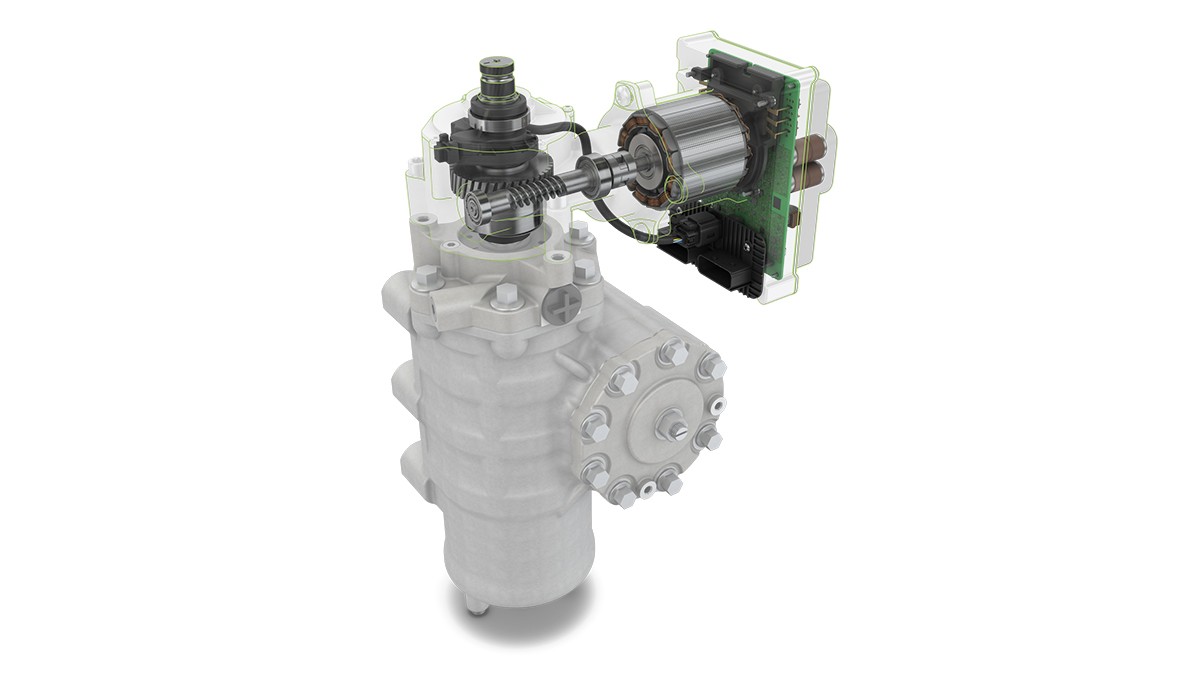
Steer-by-wire solutions
Development of the Schaeffler steer-by-wire systems for front axles is based on advanced development of the Space Drive add-on solution . In this context, all the experience and expertise gained in following the chassis roadmap thus far is leveraged to offer front wheel steering (FWS) ─ an innovative, integrated by-wire steering system for volume applications.
Space Drive
Ever since 2018, Schaeffler has been working to further develop and advance the innovative Space Drive concept. This technology was originally pursued for individuals with physical disabilities so that they could assume full control of a vehicle electronically. Vehicles outfitted with the Space Drive system have to date driven over one billion kilometers without issue. Schaeffler has also demonstrated the potential of the technology in motorsport, such as in the GTC series, the 24 Hours at the Nürburgring, the DTM and ─ at a future date ─ in the DTM Electric [3].
In a motor vehicle, the steering system represents one of the systems whose functional operation is of fundamental relevance to road safety. Space Drive fulfills the resulting technical requirements by integrating an electronics architecture with dual redundancy: Should one component lane fail, two backup systems provide highest intrinsical availability of the steering function.
The current development stage ─ the Space Drive 2 add-on ─ will be individually approved for road use in conjunction with the vehicle. In the subsequent generation of the system ─ the Space Drive 3 add-on ─ the overall concept will be optimized in terms of sensorics and efficiency of drives for break and steering actuation. The focus of this further development, however, will be not only on the aforementioned functional optimizations as it also pursues the design target of homologating the system. This will be achieved by meeting the Automotive SPICE requirements throughout the entire development process. In so doing, Schaeffler simplifies integration, thereby making it possible to rationally outfit small-scale series with Space Drive technology.
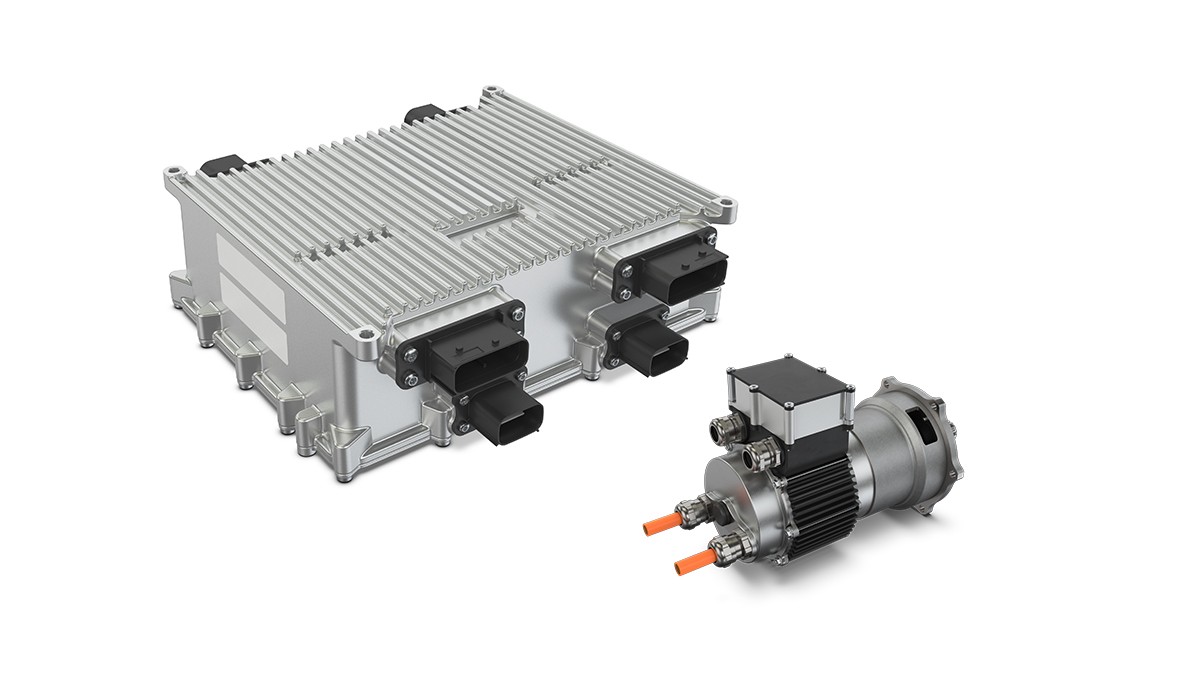
Fully integrated by-wire steering system
The front wheel steering system (FWS) from Schaeffler represents the company’s approach to developing a fully integrated steer-by-wire system for volume applications (Figure 9). To this end, the system is designed as a full replacement for the mechanical steering column on future vehicle platforms and offers maximum integration flexibility. It comprises a module for steering the front axle, the road wheel actuator (RWA) and a steering actuator ─ the hand wheel actuator (HWA). The steering angle is determined in relation to the steering wheel by the HWA. This serves as the basis for the steering actuation realized by the RWA. The HWA also provides feedback to the driver in the form of simulated force feedback from the RWA.
One of the development focal points of the FWS is the degradation concept of the SbW system. A safe system state is not sufficient in case of a first failure. Instead, steps must be taken to ensure that the steering function is maintained with acceptable availability. After second failure the function may degrade but still ensures that the vehicle comes to a safe standstill ─ i.e. that passengers and other road users are not exposed to any danger. To implement the FWS architecture, Schaeffler draws on the extensive experience gained with Space Drive in the field of functional safety.
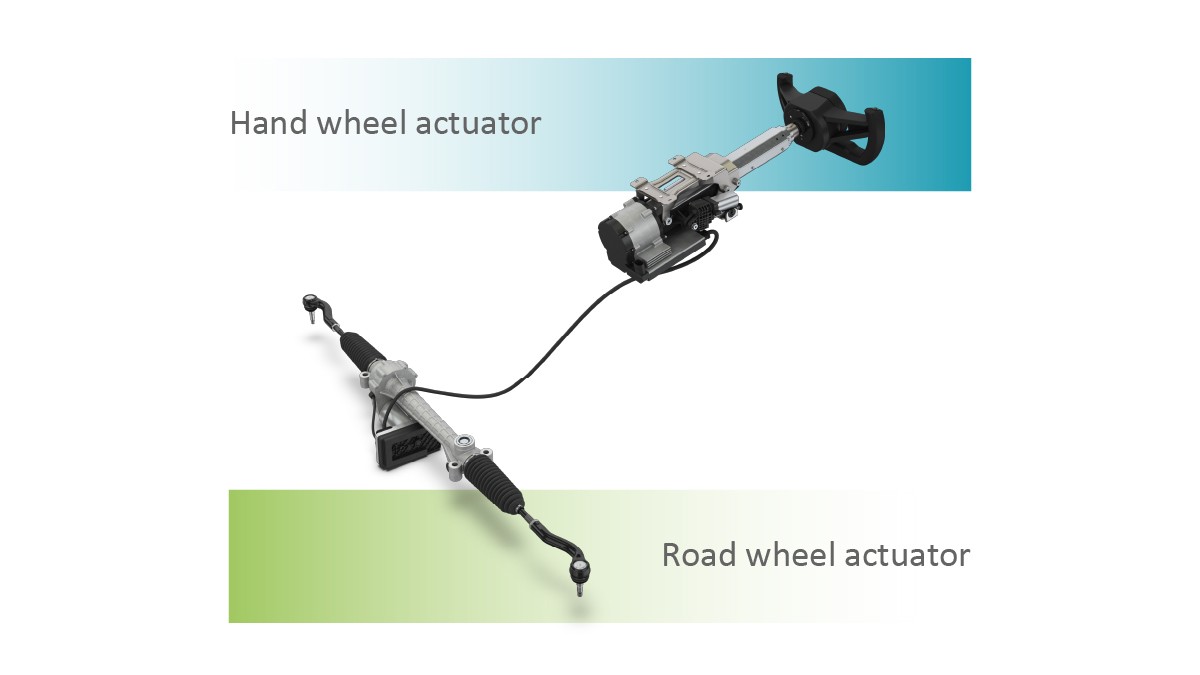
Hand wheel actuator
The hand wheel actuator (HWA) (Figure 10) connects to the steering wheel and transmits the current steering wheel angle to the RWA via the on-board vehicle electronics. The HWA also provides the driver with the necessary force feedback for vehicle directional guidance. To accommodate vehicle concepts with highly automated driving functions (SAE L4), the HWA is being developed in versions with a large traversing path by which the steering wheel can be retracted into the dashboard. HWA versions without this function are also planned for vehicles without full automation. To optimally implement these different tasks, Schaeffler has divided the HWA into two subsystems. While the force feedback actuator (FFA) determines the steering wheel angle and generates the force feedback steering wheel forces, the motion mechanism for the steering wheel is combined in the electrically adjustable column (EAC). Schaeffler is also collaborating with Autoliv to analyse interaction between the stowable HWA, passive safety as well as interior design and to drive innovations from an holistic approach. To this end, analyses are conducted to determine how the protective effect of the airbags can be safeguarded with new interior concepts, the steering wheel retracted and new steering wheel designs in place (e.g. steering yokes).
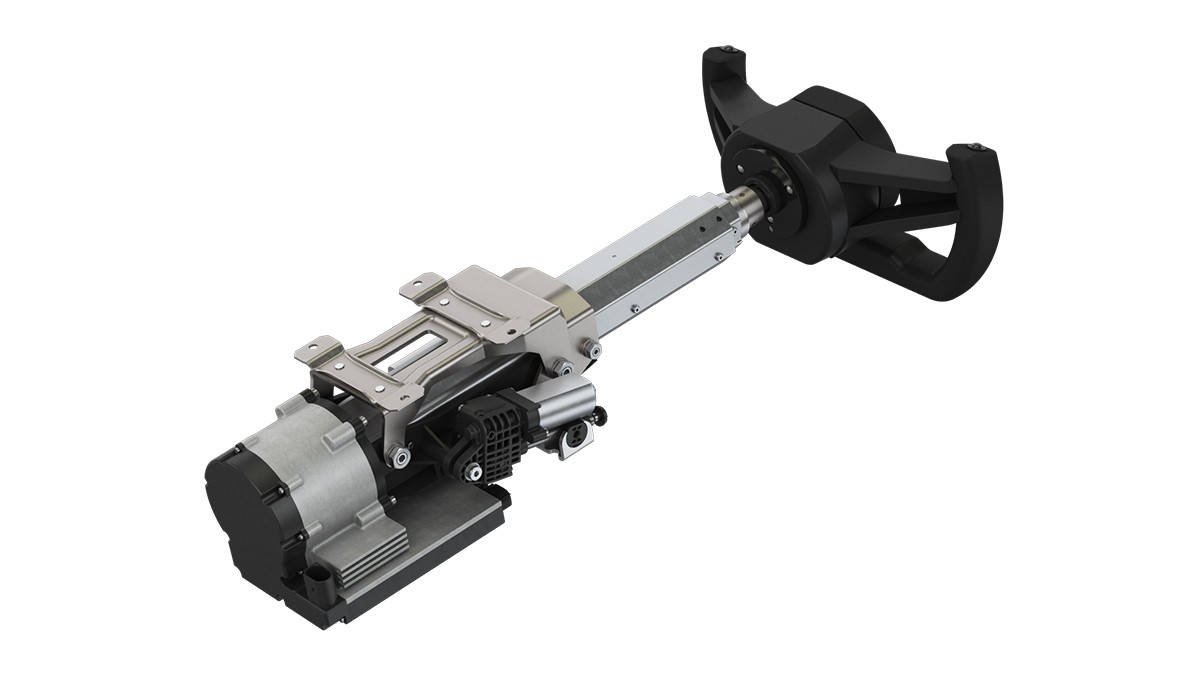
Electrically adjustable column
As mentioned, the HWA is alterable via the electrically adjustable column (EAC) (Figure 11). The kinematic of the system ensures ─ for today ─ a very large travel range beyond 200 mm. In developing the EAC, Schaeffler leverages its extensive experience in conceptual design, engineering and the manufacture of sheet metal components as well as their subsequent mass production assembly know-how. The core element of the EAC comprises steel sheets joined to form a robust octagonal tube. The dimensions and design of the structure are proofed using various calculation methods such as multi-body simulations and modal analyses. Schaeffler also uses simulation exercises to verify the crash performance and NVH characteristics prior to verifying them in hardware tests.
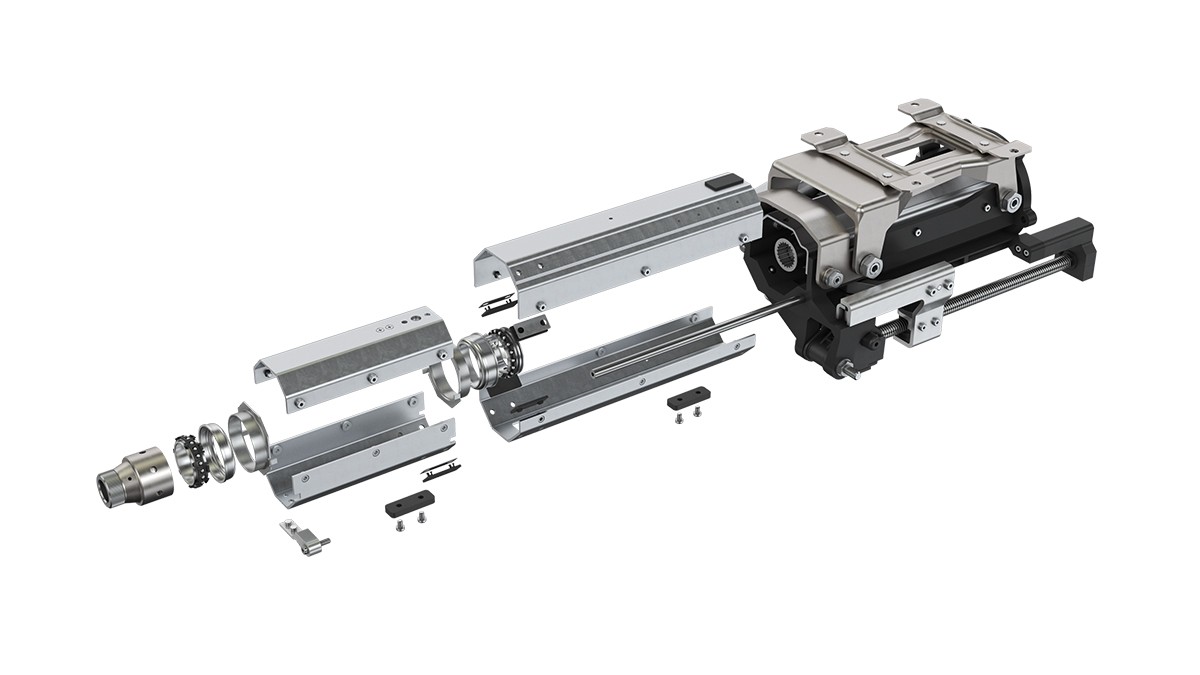
One special technical aspect of the EAC is its large, solid angular contact ball bearing in which steel components are fitted in place of the customary plastic elements to guide the steering shaft. The bearing reliably absorbs the forces and torsional moments initiated by the steering wheel. Thanks to the zero backlash and rigid support of the steering shaft as well as low friction levels, the bearing also helps ensure that the vehicle can be easily and precisely steered.
Retraction (forward/backward) of the steering wheel is realized using a double extension mechanism. The mechanism comprises tubular elements that are arranged inside of each other, are interlocked and retract/extend in a defined manner during the adjustment routine. The operating principle behind the locking effect is based on a rolling bearing mounted in the inner tube that presses against the outer tube by way of a spring force. There, it mechanically engages in recesses, thereby blocking the axial movement of the tubes. When the steering wheel is traversed, the lock releases the tubes in succession until the required position is reached, at which point the next sequence of the lock is activated. The combined design of an angular contact ball bearing with a locking device allows Schaeffler to design an EAC using just two drives.
The tubes are supported by special linear ball bearings. These bearings comprise a disc-shaped cage that guides the balls of the bearing assembly on an oval raceway. This overall design enables zero backlash as well as smooth and noise-free axial movement of the tubes.
Force Feedback Actuator
Figure 12 shows different characteristic steering wheel torques and speeds of a conventional steering system that occur when driving. Steering torques are particularly high when the wheel reaches the limit stop, the driver leans on the steering wheel when exiting the vehicle or the wheels “kiss” the curb and momentarily block the steering. The actuating speeds achieved in these scenarios are, by contrast, comparatively low. The driver can also execute very fast steering movements during a double lane change, for example. The torque required for this is, however, low. If the steer-by-wire system should feel like a conventional steering rack, the force feedback actuator (FFA) must reflect these actuating torques and steering angle speeds as accurately as possible. As actuating torques increase, however, so too does the effort required to generate them since the system power pack must be dimensioned larger.
This is why Schaeffler has two different FFA concepts currently in development, which are being advanced to make them ready for production implementation (Figure 13). The first is a compact system with direct drive. With a maximum feedback torque of 15 Nm, it covers the majority of requirements shown in Figure 14. The torque-generating motor is arranged axially to the steering shaft at the back of the FFA so that the system can also be integrated in vehicles with minimal installation space. Schaeffler is also working on a high-performance FFA whereby the electric motor induces feedback torque using a worm gear. This also permits high torques of up to 35 Nm to be generated, thereby allowing the system to cover all the scenarios pictured in Figure 14. The package is, however, disadvantageous with respect to the fact that the motor is mounted on the side of the FFA.
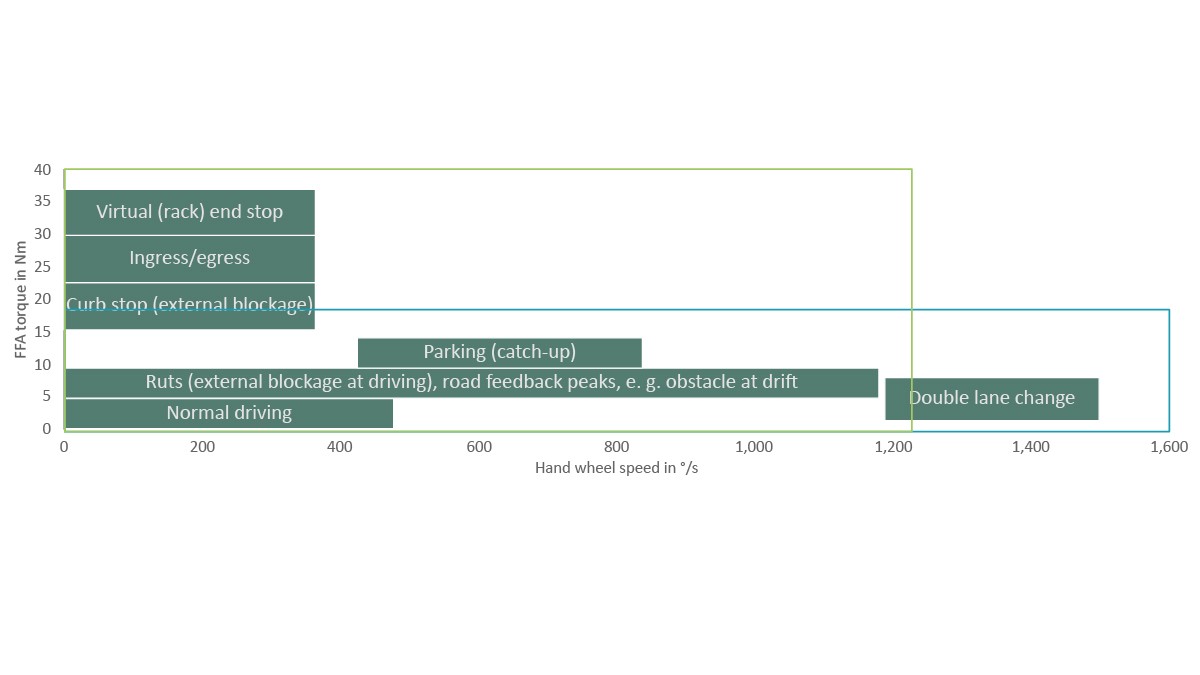
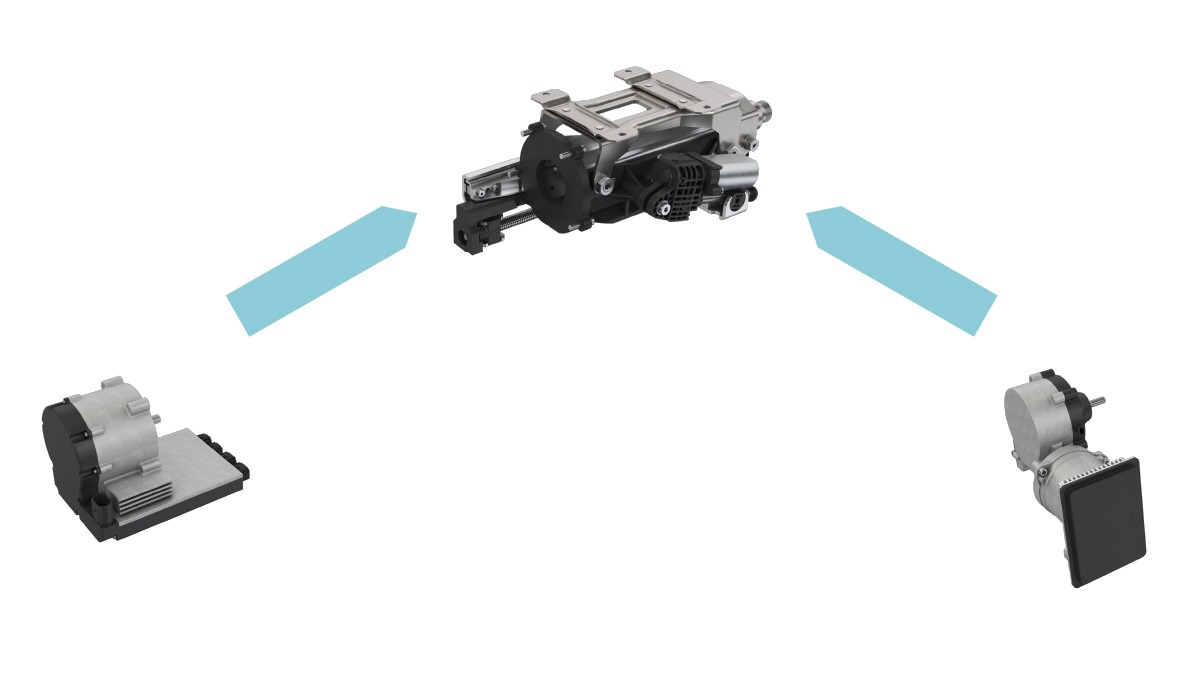
Road wheel actuator
In vehicles with FWS, the mechatronic road wheel actuator (RWA) (Figure 14) replaces the conventional steering gear. To this end, Schaeffler is developing a modular system based on two different approaches for the mechanicals and power pack to cover the broadest possible range of market requirements.
As for the mechanicals, an RWA with pinion gearing is being developed together with a partner for the smaller and medium-sized vehicle categories. This unit achieves a traversing range of 60 to 90 mm with an adjustment speed of 40 to 60 mm/s. For larger vehicle categories such as luxury class sedans and pick-up trucks, a ball screw drive is used to provide the required actuating forces. The traversing range in this scenario is +/-110 mm with an adjustment speed of 140 mm/s. This variant is developed in house. To this end, Schaeffler leverages its many years of experience amassed in developing and manufacturing ball screw drives. Some of these units are already being installed in EPS steering systems by tier 1 suppliers.
The Schaeffler modular system also offers versatility with regard to the power pack. Both a 12 V and a 48 V variant are being developed to cover all future vehicle architectures.
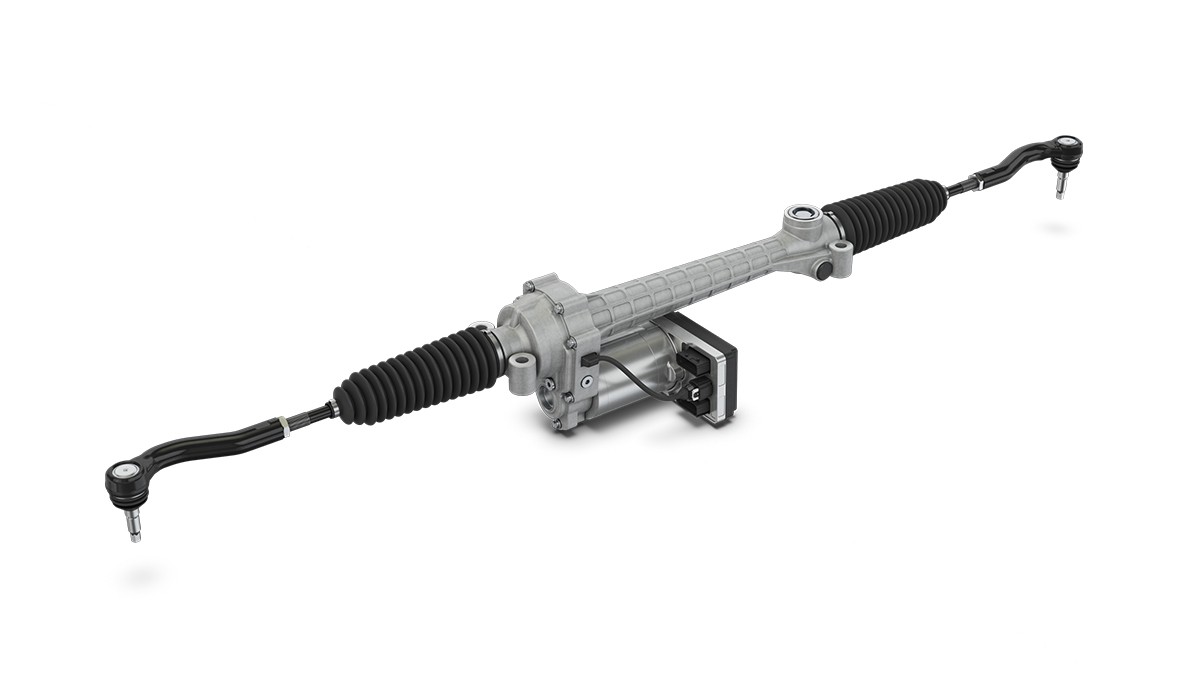
Summary
Schaeffler is addressing future challenges with respect to vehicle chassis designs by leveraging a focused development strategy. The previous milestone following mechanical components was the electromechanical active roll control system in 2015. The mechatronic rear-axle steering system (iRWS) will go into volume production in 2022. In 2023, Schaeffler will start volume production of an electrohydraulic steering system (EHPS) for commercial vehicles.
With steer-by-wire for the front axle, Schaeffler is developing the innovative front wheel steering (FWS) system based on the Space Drive system, which is being further developed and advanced as an add-on variant. To this end, the FWS is set up as an integrated system that will fully replace conventional steering hardware. In the process, the mechatronic road wheel actuator (RWA) will replace the conventional steering gear. Schaeffler covers the different performance requirements in the numerous vehicle segments by offering two RWA systems and 12 V and 48 V versions.
The hand wheel actuator (HWA) of the FWS breaks down into two subsystems: While the force feedback actuator (FFA) determines the steering wheel angle and generates the force feedback steering wheel forces, the motion mechanism for the steering wheel is combined in the electrically adjustable column (EAC). Schaeffler is currently devising two different FFA concepts ─ a compact system with direct drive and an especially high-performance FFA with worm gear. The design of the EAC focuses on the longest possible outward travel of the steering wheel, which is achieved by an innovative double extension mechanism. In fully automated vehicles, this design facilitates operating concepts whereby the steering wheel fully retracts into the dashboard during highly automated driving mode to create additional space for the driver.
[1] Böhm, A.; Kraus, M.: The Rolling Chassis from Schaeffler Spearheads New Mobility Solutions. Bühl: Schaeffler Kolloquium, 2022
[2] Steer-by-Wire auf dem Weg zur Großserie. In: ATZ extra “Innovationen für eine nachhaltige Mobilität”, 2019
[3] Schröder, J.; Kohl, D.; Störkle, D.: Development of a Vehicle Concept and Electric Drive System for the All-new Racing Series DTM Electric. Bühl: Schaeffler Kolloquium, 2022