The Rolling Chassis from Schaeffler Spearheads New Mobility Solutions
Alexander Böhm | Dr. Manfred Kraus
Electrification, automated driving, connectivity and sharing offers provide the ideal basis for new mobility concepts utilizing driverless shuttle systems. To enable their economical operation and make them marketable, Schaeffler continues to drive forward the development of autonomous transport solutions together with its partner Mobileye. To this end, Schaeffler is creating a "rolling chassis" that combines all driving function components such as the drivetrain, brake, steering system and battery in modular fashion. By leveraging partnerships for overall vehicle integration and driving automation, complete vehicles for passenger and freight transportation can be realized based on the rolling chassis ─ from robo taxis to autonomous delivery vehicles. When supplemented with intelligent infrastructure systems and connectivity options, comprehensive mobility solutions can be implemented applying this strategy.
- Development of urban transport
- Autonomous transport systems
- Development strategy for new forms of mobility
- Wheel hub motors
- E-axle
- By-wire steering system
- Schaeffler corner module
- Central control of the rolling chassis
- Modularity and scalability
- Vehicle platform
- Robo shuttle ecosystem
- Summary
- Literature references
Development of urban transport
If you review how mobility has evolved over the past 150 years, you quickly realize that the much-cited concept of transforming transportation is not a phenomenon just limited to modern times. As early as the end of the nineteenth century, a shift in mobility emerged that was driven by traffic-related environmental problems, but of a different sort. Many cities, in fact, were on the verge of suffocating in the dung left behind horse-drawn carriages. And so at the turn of the century, the automobile was marketed as a way to do without horses while still getting to your destination, thus keeping cities clean. It goes without saying that automobiles gained the upper hand over horses worldwide in the years that followed (Figure 1).
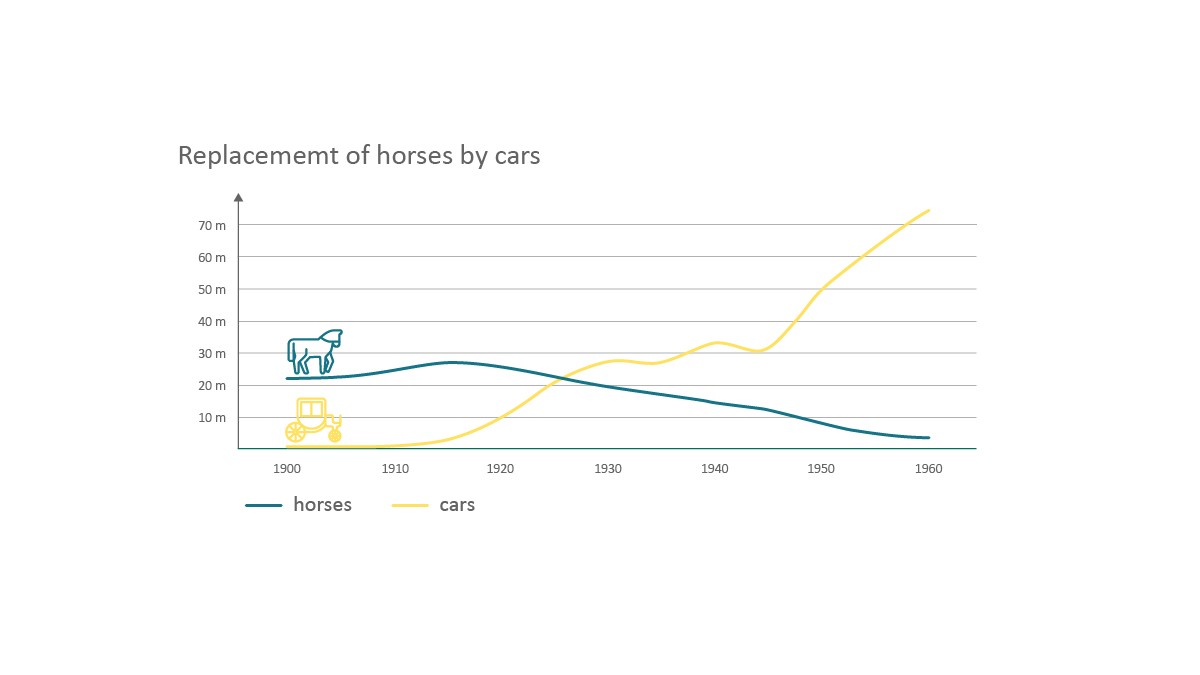
Certain parallels to the present day become apparent as current environmental pollution also calls for a radical technological leap in mobility. In Germany, road traffic accounts for around 20 percent of total CO2 emissions [1]. New, clean technologies will therefore soon replace the internal combustion engine, just as the latter waved goodbye to the horse back in the day. This change does not solve all of the problems faced by today's mobility, however. One issue that remains is the large amount of land space required for parking ─ particularly in urban areas. In Germany, the parking space set aside for vehicles is equivalent to an area encompassing some 270,000 soccer fields. Another aspect is the high number of traffic accidents. Worldwide, over 1.3 million traffic fatalities occur per year. Also, traffic jams not only damage the economy, but lead to additional direct and indirect costs totaling some Euro 80 billion.
These problems cannot be solved by merely "switching" to electromobility, and it is foreseeable that they will become more pronounced in the future. According to United Nations projections, 68 percent of the world's population will live in urban areas by the year 2050 [2]. To put things into perspective, in 1950, this figure was only 30 percent. As such, the number of urban dwellers worldwide has experienced rapid gains since 1950 ─ with 751 million ─ to 4.2 billion in 2018. By 2050, another 2.5 billion will be living in cities. Many metropolises are therefore already actively counteracting additional booms in traffic by trying to reduce the number of privately owned vehicles and promote other transportation concepts. One such example is Paris. The French capital is currently attempting to transforming itself into a so-called "15-minute city", whereby all basic needs can be met within this time window by traveling on foot or by bicycle from home (Figure 2). Other cities are making plans to introduce bonus/penalty systems for passenger cars or reduce their sheer number by limiting legal registrations or parking spaces.
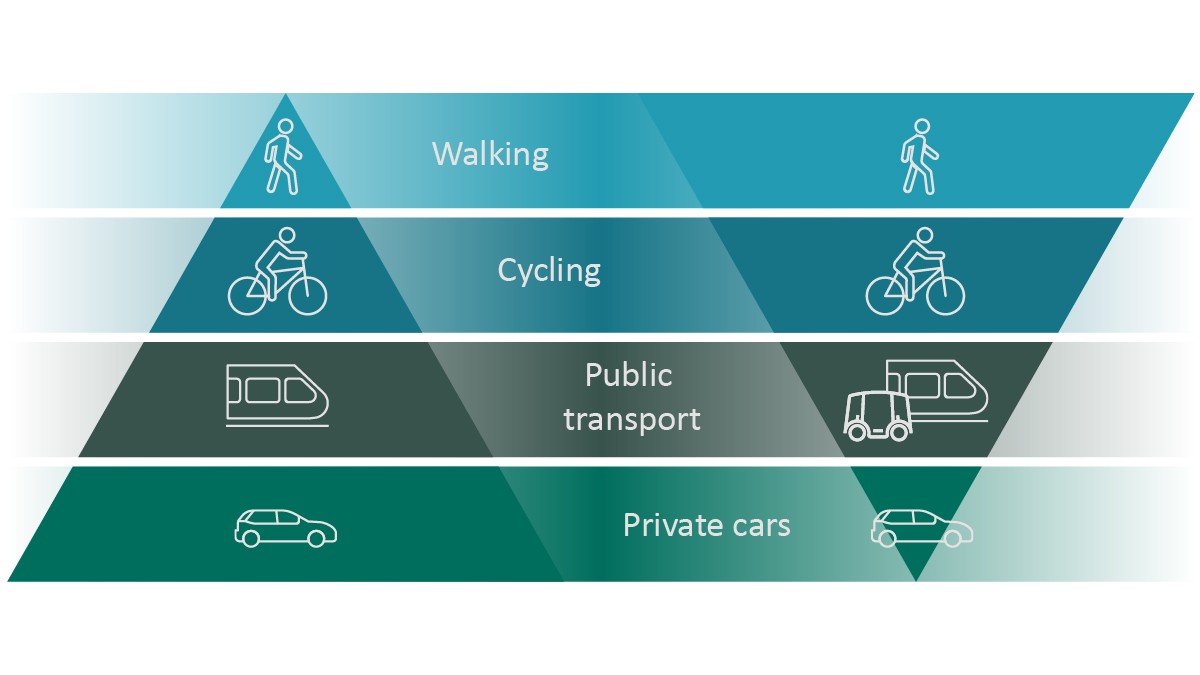
Autonomous transport systems
The automotive industry is also addressing these challenges by developing new mobility concepts that link connectivity, electrification, automated driving and sharing services. To this end, Schaeffler presented its Schaeffler Mover concept back in 2018 [3] (Figure 3). This vehicle is designed to transport many individuals quickly and in comfort while operating at high efficiency and being kind to the environment. The concept behind the transport system leverages SAE level 4 automated driving (high degree of automation). As shown by a study jointly conducted by the Boston Consulting Group and the University of St. Gallen in 2020, a change in the traffic mix through the integration of autonomous robo taxis could reduce urban emissions by a minimum of 12 percent, while freeing up 35 percent of available spaces and reducing the number of accident-related fatalities by a whopping 37 percent. Roadway congestion will also be reduced.
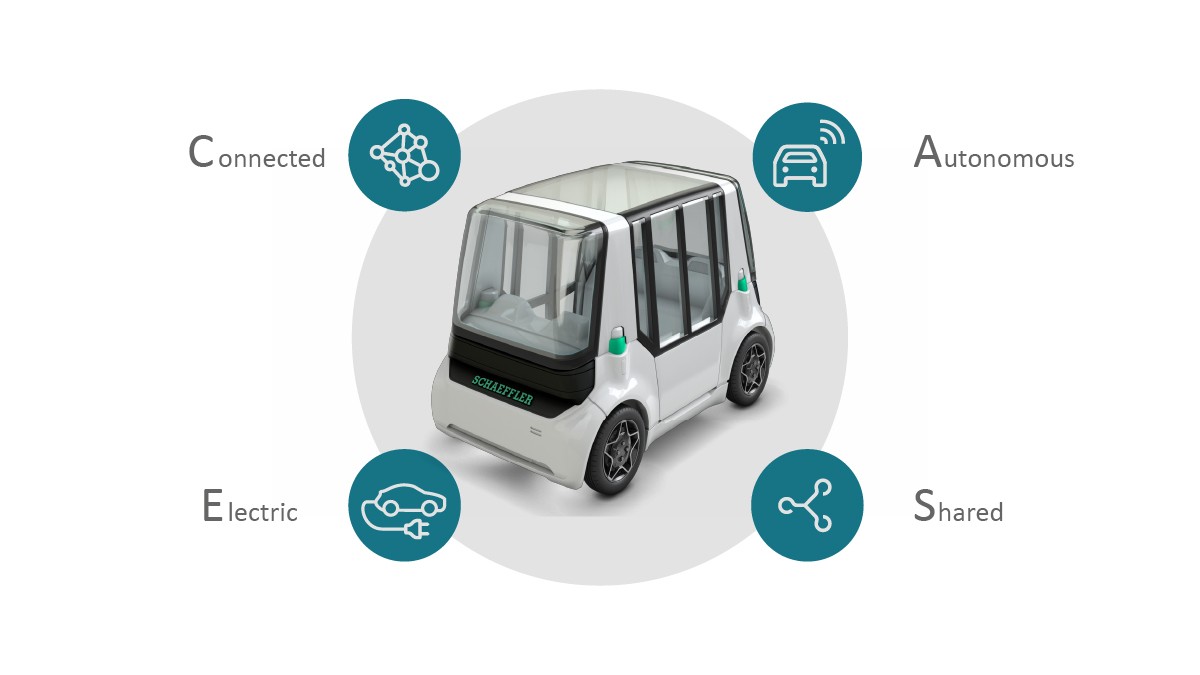
Just under 60 pilot projects with autonomous shuttle systems have already been managed in Germany alone. There are still a number of hurdles to overcome before the vehicles can be economically used in real-world operations. To date, the projects have been particularly limited by the fact that it was not legally possible to operate the systems on public roadways without accompanying safety personnel to manually take control over the vehicle in dangerous situations. In 2021, a new law on autonomous driving established the legal framework in Germany for highly automated motor vehicles to be driven in defined operating areas on public roads nationwide [4]. Germany is thus assuming a pioneering role in the autonomous driving scene, and other countries are expected to soon follow.
As numerous feedback from operators of the shuttle systems in the pilot projects has indicated, there are two major technical limitations adding to the legal hurdles.
- In many of the pilot projects, the vehicles are used on previously measured routes. Further, they are controlled by the computer making target/actual comparisons of the driving trajectory or utilize magnetic strips. In other words, the vehicles drive on a "virtual track". As such, they cannot respond to necessary changes in the driving trajectory in order to avoid a vehicle parked at the side of the road, for example. In such a scenario, the electronics would simply stop the vehicle in its tracks for safety reasons.
- Fully autonomous vehicles are still frequently designed for a limited range of use and are approved for only low speeds of around 25 km/h. They also do not have critical active safety systems such as ABS as well as sufficiently redundant control systems.
Together with its partner Mobileye, Schaeffler will drive forward solutions on both of these fronts. Here, the objective is to facilitate economical operation of autonomous shuttle systems, thereby making them ready for the marketplace. In this context, Schaeffler anticipates that every tenth vehicle on the road could be an automated transport system in the near future. Robo shuttles will therefore not replace conventional passenger cars, but instead add to the mobility offering available to the public.
Development strategy for new forms of mobility
Figure 4 illustrates Schaeffler's development strategy when it comes to new forms of mobility. The underlying basis is cemented by product innovations in drivetrains and steering systems. To this end, Schaeffler is developing a "rolling chassis" that combines all driving function components such as the drivetrain, battery, brakes and steering system in a modular and scalable fashion. Sophisticated drive-by-wire technology enables safe operation on public roads. By leveraging partnerships for overall vehicle integration and driving automation, complete vehicles for passenger and freight transportation can be realized ─ from robo taxis to autonomous delivery vehicles. When supplemented with intelligent infrastructure systems and connectivity options, comprehensive mobility solutions can be implemented such as those of mobility providers serving the public or private sectors.
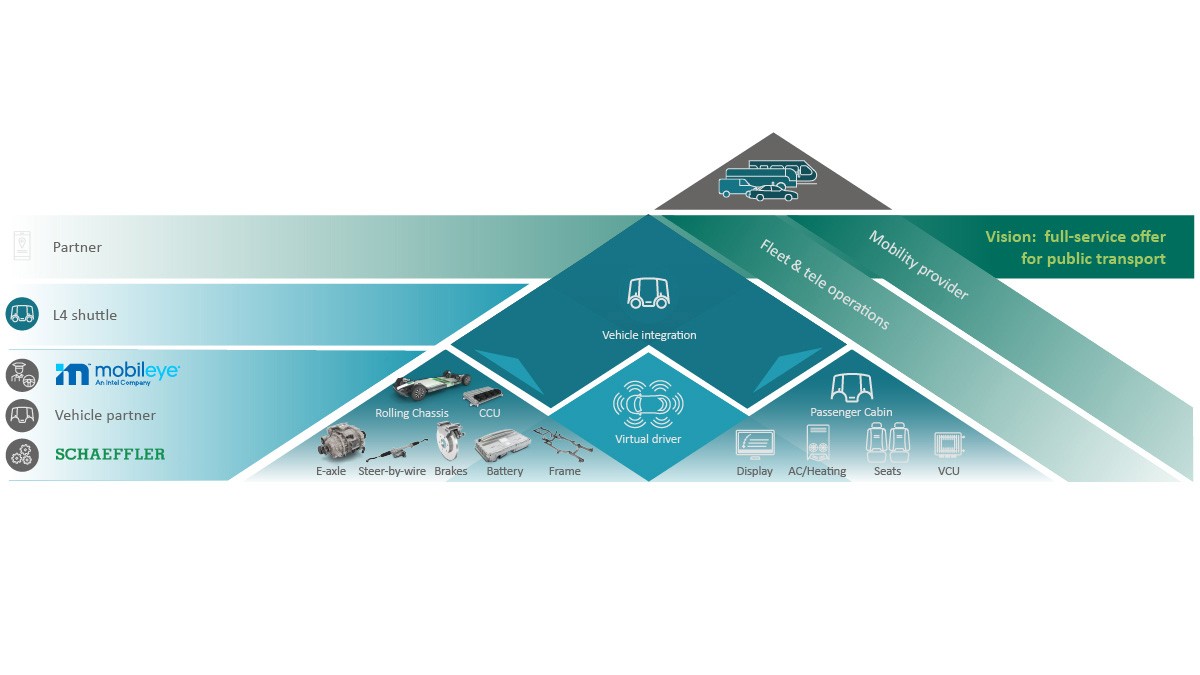
The individual components of the development pyramid shown in Figure 4 are described in greater detail below, starting with the Schaeffler products for drivetrain and steering systems, through to their integration and the functional combination of individual systems to form a rolling chassis.
Wheel hub motors
The wheel hub motors currently being developed at Schaeffler primarily comprise the stator and rotor motor components, the reduction gearbox and an integrated braking system Figure 5. The inverter is not integrated but can be accommodated in the vehicle in versatile fashion. One inverter controls one to two wheel hub motors, depending on the application in question. The drive power of the motors directly correlates to their size and can be scaled modularly. The power range of the motors extends from 7 to 26 kW (nominal), with a maximum output of 14 to 60 kW available for brief periods. Drive torque ratings are 730 Nm (nominal) and 1,650 Nm (maximum), respectively. An important key figure here is the torque density in the wheel which, thanks to all drive variants being integrated in a 14-inch rim, equates to upwards of 118 Nm per inch of rim size. Due to the cooling requirements associated with the high power, the wheel hub motors are fitted with a liquid cooling system. Heat exchange with the outside air takes place via one or more coolers that are housed separately in the vehicle. Schaeffler develops wheel hub motors for electrical voltages of 48 and 400 V. Higher voltages are also foreseeable in the future. According to current plans, series production of Schaeffler's wheel hub motors will start in 2023.
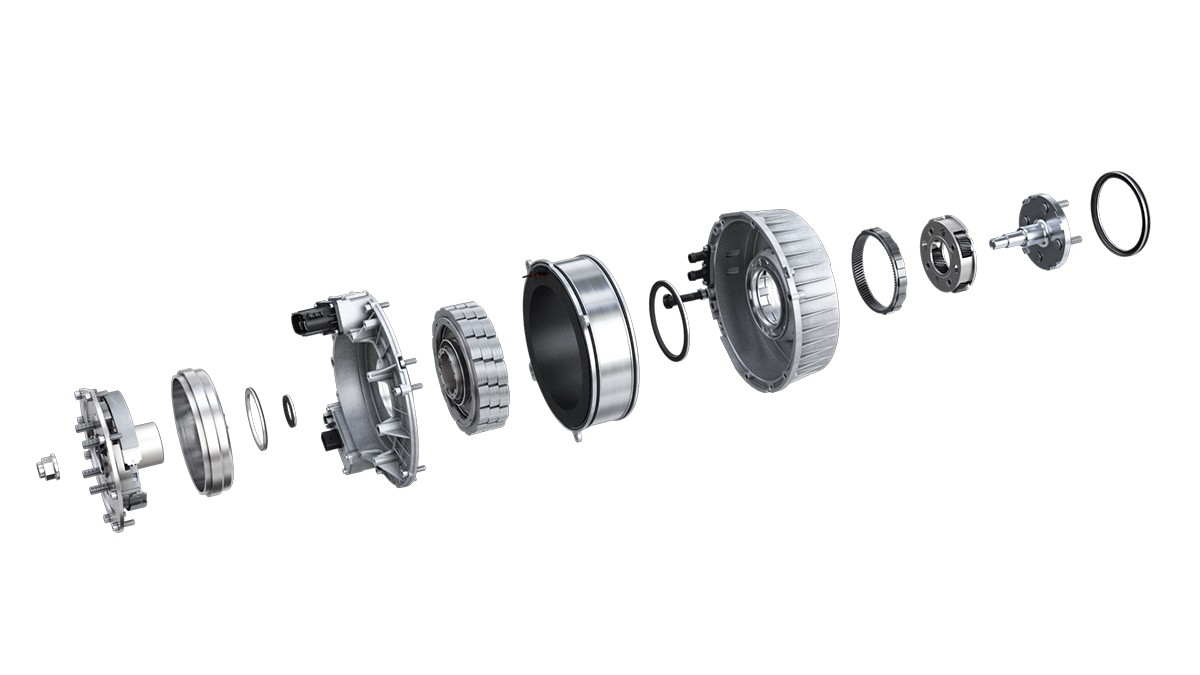
E-axle
The rolling chassis can be equipped with an E-axis as an alternative to wheel hub motors (Figure 6). The electric drive motor is then positioned between the wheels and power is transmitted to them mechanically via driveshafts. A special aspect of the Schaeffler solution is the design with a spur gear differential, which allows the driveshafts to be arranged concentrically to the rotor axis of the motor to save space. All e-axles from Schaeffler used in new mobility concepts have integrated power electronics and liquid cooling. The power range is 50 to 500 kW (nominal) or 2,000 to 8,000 Nm (maximum). Schaeffler has already been manufacturing e-axles in series production since 2018 and will reach a production figure of several million units annually by 2027.
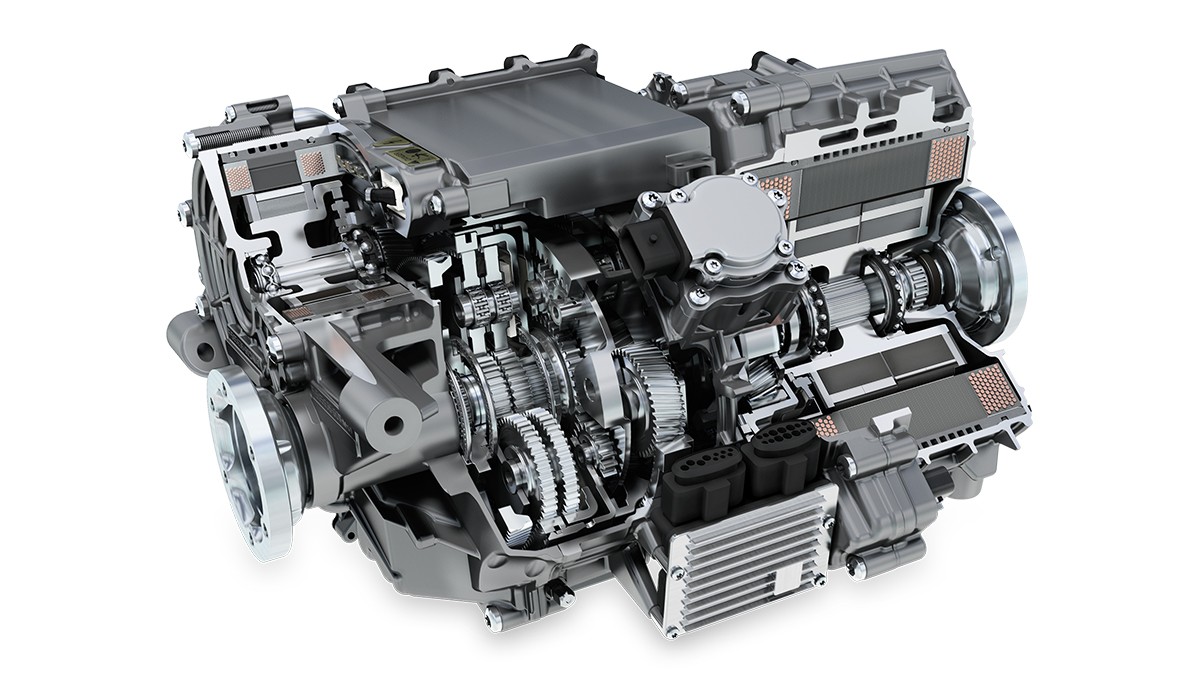
By-wire steering system
Driverless, electronically controlled vehicles require a steer-by-wire system in which steering commands are no longer transmitted mechanically by the steering column and steering wheel, but instead electronically. In implementing a high-performance, safe modular system, Schaeffler is following a stringent innovation plan that includes mechatronic rear-axle steering (intelligent rear wheel steering, or iRWS) and power packs at the component level (Figure 7) [5]. This development incorporates the extensive knowledge gained during the implementation of the Space Drive steer-by-wire system from Schaeffler. A power pack comprises the electric motor that applies the steering forces and the associated power electronics. For rolling chassis applications, the motor unit can be combined with one or more spur gear stages to optimally adapt the system to the speeds and steering torques required by the application. These drives, which are compatible with a system supply voltage of 12 V or 24 V, deliver a power rating of up to 880 W.
The power electronics used maintain an appropriate redundancy level in the power and logics areas and are thus prepared to meet the functional safety requirements of future steer-by-wire applications. The electric motors, for example, can be operated using a double winding to safeguard failure protection in the event of defects. Schaeffler has designed the power packs so that project partners can combine them with their own mechanical steering components when implementing joint rolling chassis developments. Schaeffler's modular steering system thus facilitates flexible application in the field of autonomous shuttle systems.
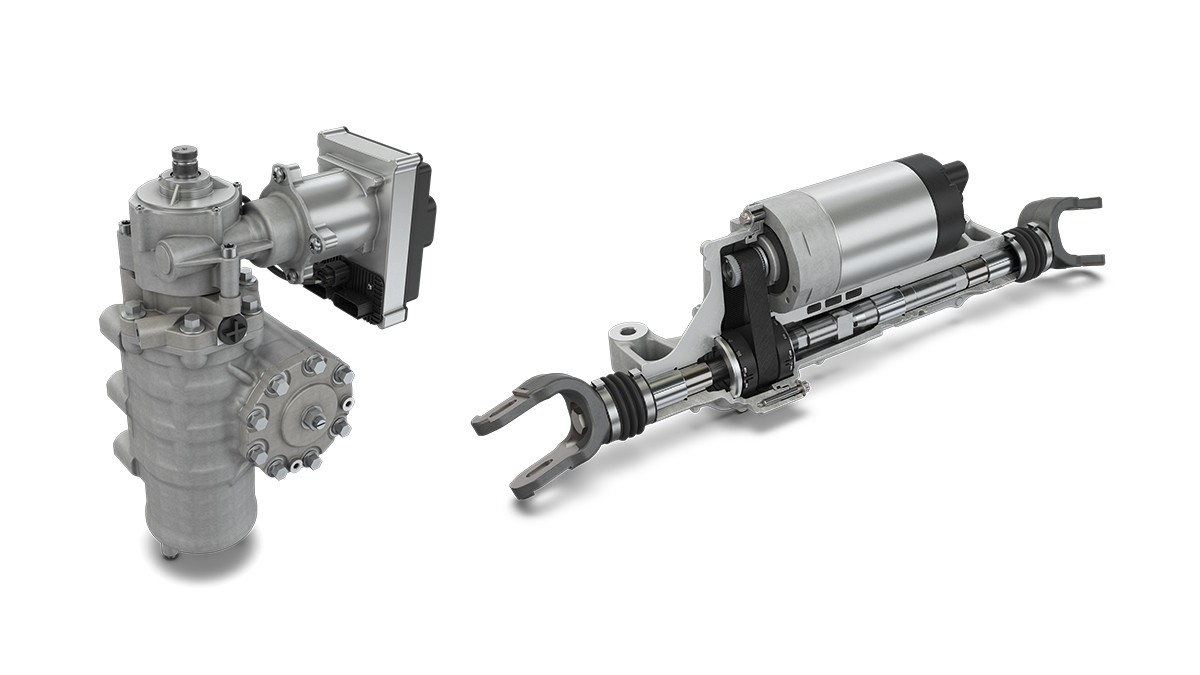
Schaeffler corner module
The Schaeffler corner module specially developed for the rolling chassis comprises the wheel suspension with suspension componentry. The actuator for the electromechanical steering system and a wheel hub motor can also be integrated. The latter eliminates the need to use conventional driveshafts. This, in turn, lets the available vehicle space be used more efficiently for greater transport capacity. With the pronounced steering angle of the Schaeffler corner modules of -90 to +45 degrees, the vehicle can maneuver effortlessly when traversing narrow streets. And when four Schaeffler corner modules with integrated wheel hub motors are fitted to the vehicle, even side parking and turning on the spot are possible.
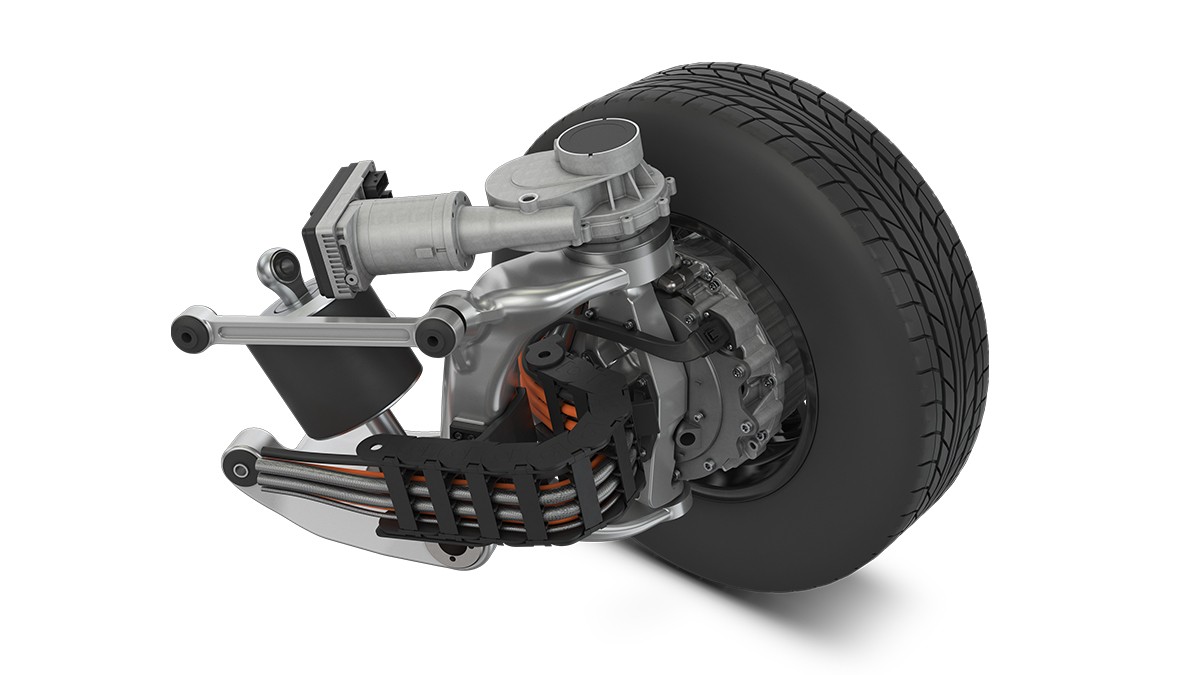
Central control of the rolling chassis
The logical further development of the integral approach implemented in the Schaeffler corner module is the systematic combination of four individual modules into a rolling chassis. The four Schaeffler corner modules are inter-coordinated by a central control unit, or the chassis control unit (CCU) (Figure 9). The CCU converts the higher-level control commands for longitudinal and lateral guidance of the vehicle into the individual control signals for the Schaeffler corner modules and controls the steering, brake and drive actuators separately for each wheel. Communication with the individual modules and vehicle control unit (VCU) takes place over two channels via the CAN bus or more powerful CAN-FD (CAN with flexible data rate). The input signals of the CCU come directly from the VCU, ECU, controller for the automated driving function (AD Control) or a control unit (sidestick) in the vehicle to perform manual driving maneuvers during service work, for example. In addition to Schaeffler corner modules with a wheel hub motor and integrated steering actuator, the versatile design of the CCU architecture can also control drive topologies with an e-axle and centrally arranged steering in the center of the vehicle (Figure 10).
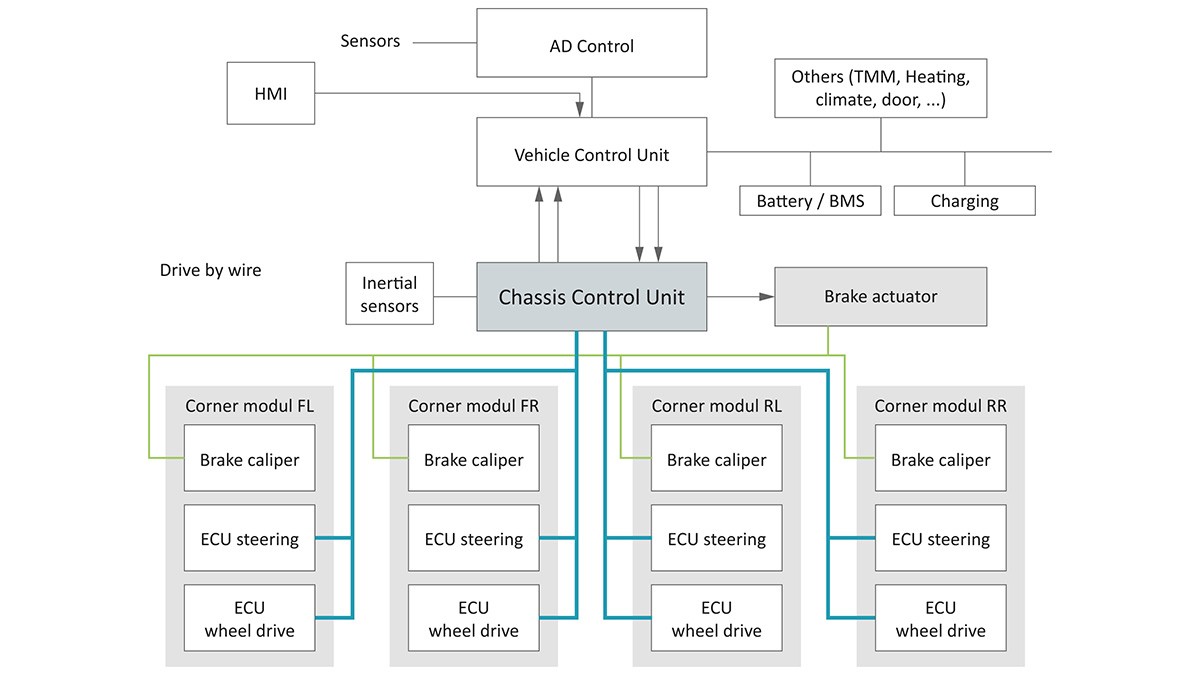
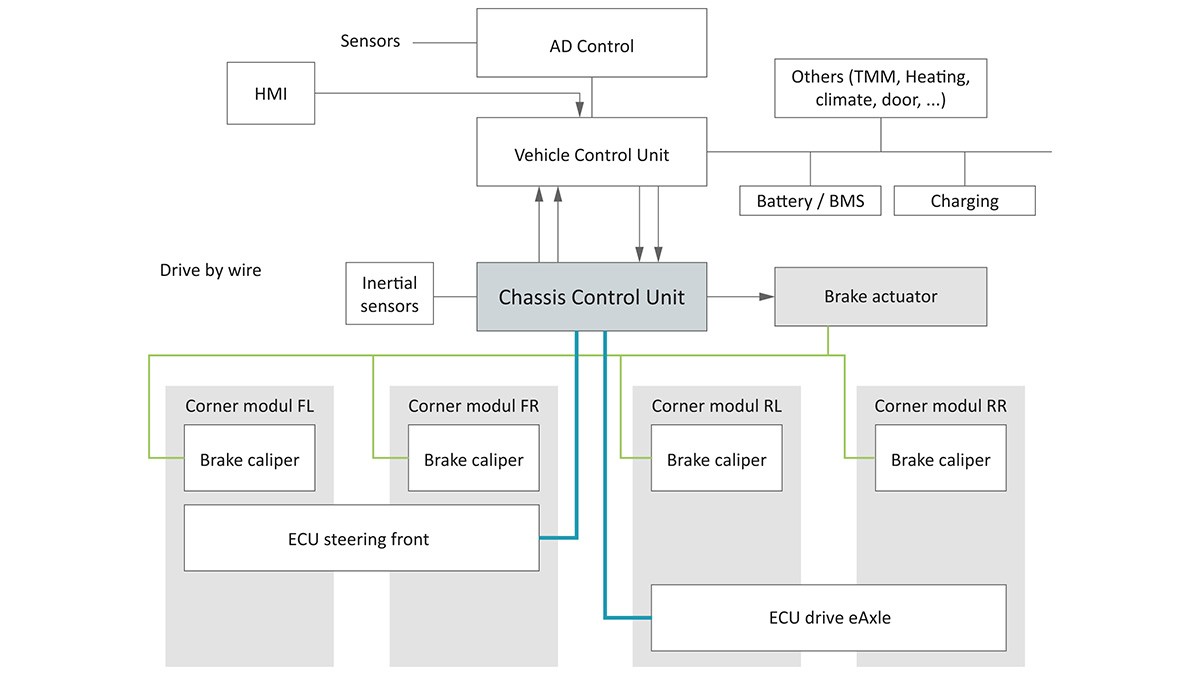
Developing a central CCU Schaeffler is reflecting a large number of customer wishes. In this context, numerous feedback and practical implementation examples have pointed to a central interface to the rolling chassis as being the key to enabling straightforward integration in different customer-specific vehicle architectures, thereby making it very desirable.
To develop the CCU architecture, Schaeffler leveraged the knowledge gained with the space drive technology in more than ten years in field experience and over 1 billion kilometers. This knowledge is also actively applied to the design of the safety concept for the rolling chassis. Complete failure of the braking and steering functions is prevented by both a redundant control architecture and physical redundancy of the actuators. This approach is referred to as "fail operational" since the system continues to operate even in the event of a failure. Faults at one functional level can be assumed by the second level of the actuators. For example, if a steering system fault occurs at one or two Schaeffler corner modules, operational safety is ensured until the vehicle comes to an emergency stop by controlling the brakes in clever fashion while steering the still functioning modules. This redundancy approach continues in the CCU, thereby enabling safe control of the actuators should a fault arise.
Modularity and scalability
When implementing the control system for the rolling chassis in software and hardware, Schaeffler placed great emphasis on a modular design. For rolling chassis customers, this results in optimal flexibility. Retaining the CCU, brake actuator and battery management and battery charging system not only helps allow them to choose between different drive concepts, but also adapt other vehicle parameters to specific requirements as needed (Figure 11). This includes the modular design of the vehicle frame, battery, braking system, steering system and wheel suspension.
Ensuring the modularity of key components forms the basis for safeguarding vehicle scalability. This allows Schaeffler to create a wide range of potential vehicle topologies that can be used as required, e.g. to design a maneuverable mover for transporting people in a downtown environment or a vehicle that delivers heavy goods over longer distances. Exceptionally good flexibility is offered by the four Schaeffler corner modules as vehicle length and width can be changed very easily.
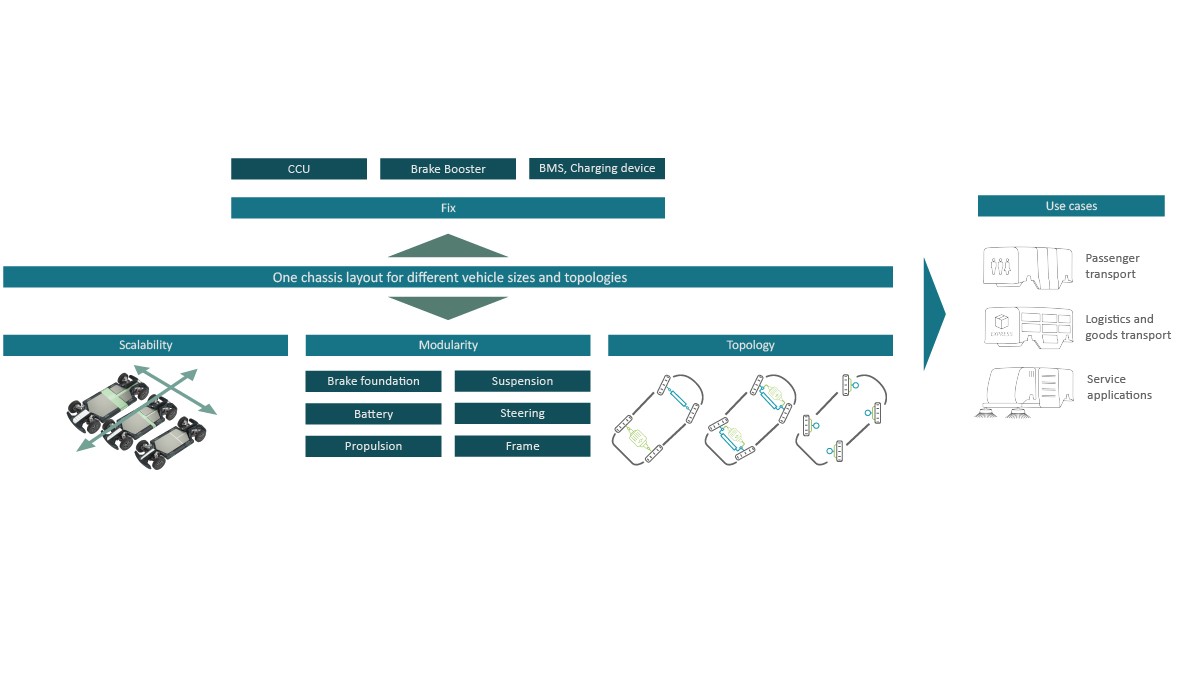
To make it easier for customers to choose the optimal system design for their requirements, Schaeffler has developed a configurator for the rolling chassis. The clearly arranged menu takes them to the respective configuration by asking targeted, logically sequenced questions (Figure 12). This series of questions covers such aspects as:
- Applications (robo taxi, robo shuttle for passenger transport or cargo mover for freight transport)
- Application environment (urban, interurban (city + rural), factory site); restriction in selectable vehicle sizes
- Selection of vehicle size and battery capacity (range calculation in relation to vehicle mass based on driving cycles and operating environment)
- Selection of Schaeffler corner modules (turning radius, suitability for special maneuvers e.g. turning on the spot or driving sideways).
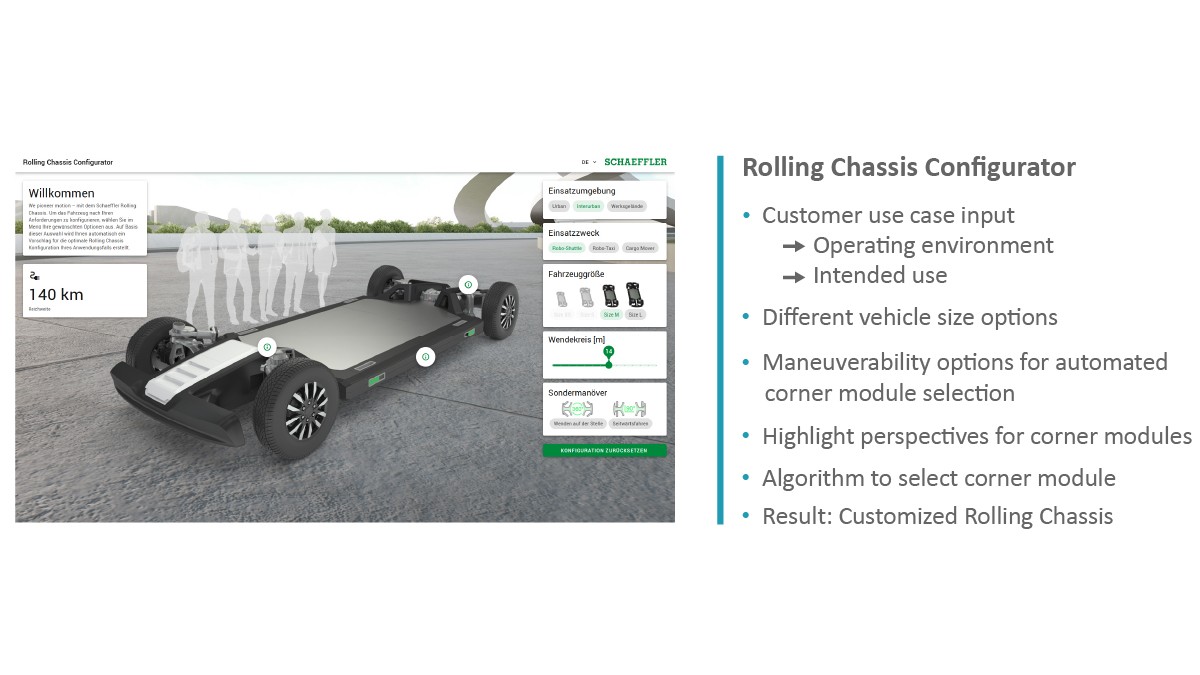
Vehicle platform
The rolling chassis currently in development at Schaeffler has a drivetrain in the form of an e-axle. The specifications are listed in Figure 13. Schaeffler is also collaborating with partner Mobileye to sharpen its expertise in the field of highly automated driving. The company is regarded as a global leader in developing technologies for vision sensors and machine-based learning, data analysis, localization and mapping for driver assistance systems as well as autonomous driving solutions. To realize the overall vehicle function, the rolling chassis is fitted with a cabin in which all sensors for the automation functions are installed. The shuttle has twelve seats and areas where passengers can stand. This gives the vehicle sufficient capacity for local public transport (LPT) use. Alternatively, ten passengers and an individual in a wheelchair can be transported. The shuttle offers barrier-free access to the vehicle via an automatically extending wheelchair ramp. To streamline battery charging, the vehicle has an automated conductive charging system. When the vehicle is parked, a current collector is lowered down onto the charging pad embedded in the floor, and the vehicle is charged via the electrical contact of the conductors. This direct physical connection enables a large amount of electricity to be transmitted with minimal loss to minimize charging times as compared to inductive charging systems, for example.
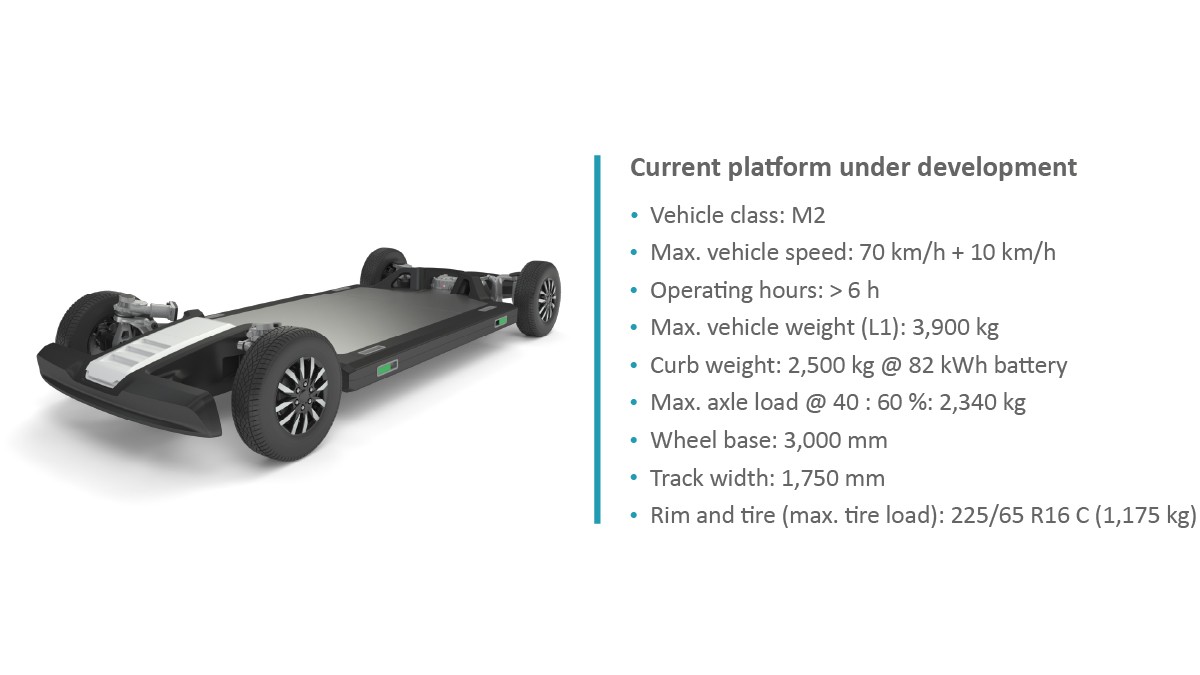
Robo shuttle ecosystem
From a conceptual standpoint, operating driverless transport systems requires an extensive ecosystem ─ the design and development of which offers great potential for innovation. This includes fleet management in addition to vehicle-related services such as battery charging and vehicle maintenance. At the customer interface, enabling vehicle access with a payment function can be designed using new app services for smartphones, which ideally are multi-modal by design and integrated into existing systems as a mobility-as-a-service offering to facilitate a seamless transition between individual types of transport. To realize a turnkey robo shuttle solution for smaller operators such as local transportation companies in particular, Schaeffler is currently seeking out partnerships for devising and operating corresponding ecosystems. As far as the charging infrastructure is concerned, Schaeffler is working on the aforementioned conductive charging system to avoid the need to handle heavy, cumbersome charging cables. Manual handling is not required for charging; the shuttle can drive fully autonomously to the charging station and be charged there.
Summary
Many metropolitan areas are actively counteracting the rise in motor vehicles in urban areas by attempting to minimize car density and promote alternative traffic concepts. The automotive industry is also addressing these challenges by developing new mobility solutions that link connectivity, electrification, automated driving and sharing services. Schaeffler already presented the Schaeffler Mover in this context a few years back. The concept behind the transport system leverages SAE level 4 automated driving (high degree of automation). Together with its partner Mobileye, Schaeffler continues to drive development forward. Here, the objective is to facilitate economical operation of autonomous shuttle systems, thereby making them ready for the marketplace. To this end, Schaeffler is developing a "rolling chassis" that combines all driving function components such as the drivetrain, brake, steering system and battery in modular fashion. Depending on power requirements, the vehicle can be driven either using wheel hub motors or an e-axle. To implement a safe, reliable steer-by-wire system for the rolling chassis, Schaeffler is developing mechatronic rear-axle steering systems as a complete system assembly and individual motor-electronics units, also known as power packs. The wheel suspension and suspension of the rolling chassis are integrated in a compact unit ─ the Schaeffler Corner Module. The Schaeffler Corner Module can also house the steering actuator and wheel hub motor, thus making it possible to flexibly adapt it to meet different customer requirements.
By leveraging partnerships for overall vehicle integration and driving automation, complete vehicles for passenger and freight transportation can be realized based on the rolling chassis from Schaeffler ─ from robo taxis to autonomous delivery vehicles. When supplemented with intelligent infrastructure systems and connectivity options, comprehensive mobility solutions can be implemented such as those of mobility providers serving the public or private sectors. In this context, Schaeffler anticipates that every tenth vehicle on the road could be an automated transport system in the near future. Robo shuttles will therefore not replace conventional passenger cars, but instead add to the mobility offering available to the public.
[1] Presse- und Informationsamt der Bundesregierung (pub.): Verkehr umweltfreundlich machen. https://www.bundesregierung.de/breg-de/themen/klimaschutz/klimaschonender-verkehr-1794672, retrieved 22 February 2022
[2] Deutsche Stiftung Weltbevölkerung (Hrsg.): Im Jahr 2050 werden zwei Drittel der Weltbevölkerung in Städten leben. https://www.presseportal.de/pm/24571/3945595, retrieved 17 January 2022
[3] The Schaeffler Mover. In: ATZextra "Innovationen für eine nachhaltige und autonome Mobilität", 2019
[4] Bundesministerium für Digitales und Verkehr (Hrsg.): Gesetz zum autonomen Fahren tritt in Kraft. https://www.bmvi.de/SharedDocs/DE/Artikel/DG/gesetz-zum-autonomen-fahren.html, retrieved 11 March 2022
[5] Feltz, C. et al.: Chassis Systems ─ Heading Toward Steer-By-Wire. Bühl: Schaeffler Kolloquium, 2022