Taking wind power to a whole new level
With energy demand growing worldwide, energy from wind is a highly available resource poised to play a key role in the market. Getting wind energy ready for the future calls for high-performance products coupled with systems know-how and an integrated approach.
Wind energy is vital to securing the world’s future energy supply and, most importantly, making the transition to greater energy sustainability. But the wind energy industry is facing a number of new challenges – namely, the need to build a new generation of wind turbines that can meet ever increasing performance and cost expectations. Interview with Schaeffler wind energy expert Andreas Mangold.
What is Schaeffler doing to meet these challenges?
The requirements facing onshore and offshore wind turbines are increasing. That’s a fact, and as market leader and strategic partner to the wind industry we need to respond to it. Our role here doesn’t end with providing pure bearing solutions. It also includes developing wind turbines further and improving their reliability so that they remain cost-effective to operate into the future. Our solution to this challenge is called closed-loop engineering. This is an integrated approach that we are using to optimize wind turbines for the new challenges facing our energy supply and to make the wind energy industry fit for the future. Closed-loop engineering in this sense hinges on close cooperation with turbine and gearbox manufacturers.
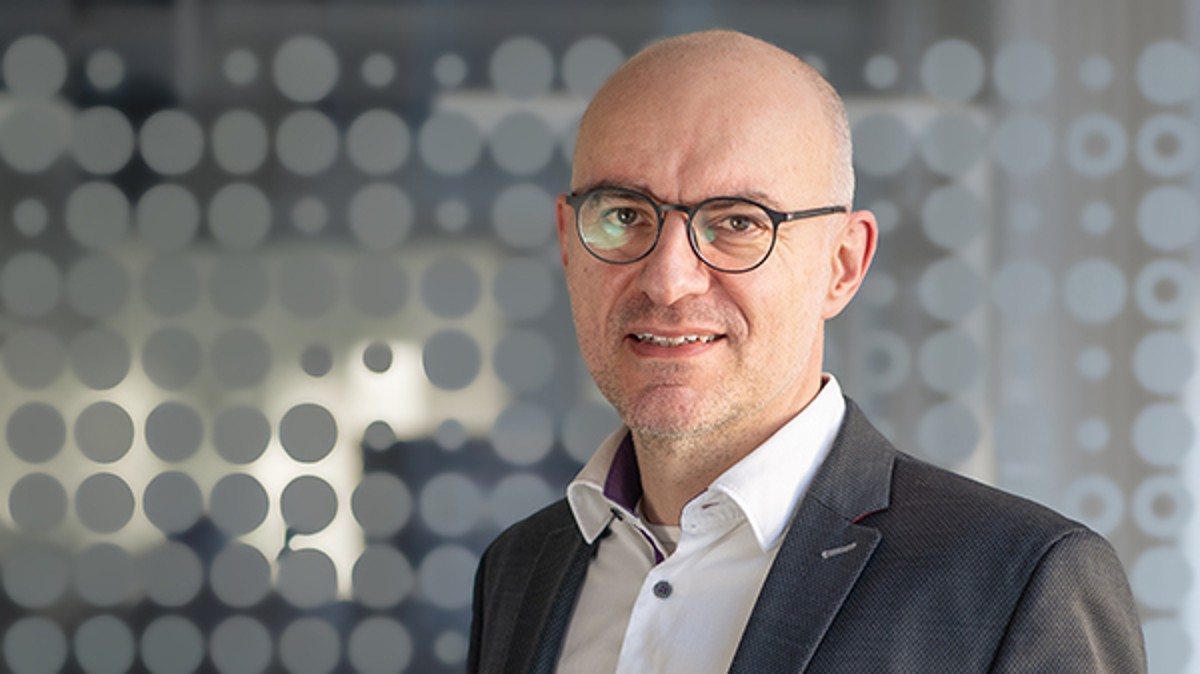
What does Schaeffler’s closed-loop engineering approach involve?
As the name suggests, closed-loop engineering is about having a closed feedback loop in which insights gained from simulation and testing, etc., are fed back into product development. For this, we undertake extensive system simulations, testing under realistic conditions, and field measurement campaigns. We then use the insights gained to continuously improve the cost-effectiveness and efficiency of our products. Our closed-loop engineering approach starts with calculation and simulation programs. This involves the use of multi-body simulation programs to generate realistic models of individual rolling bearings or even entire drive trains. The second element of our engineering loop involves testing our bearing systems under realistic conditions using test benches. These tests give us insights into the relevant forces and factors at play in wind turbines. And the third element is field monitoring and measurement. The results of these measurements either validate the original design parameters from the simulation process or, failing that, they are fed back into the simulations as a starting point for further optimizations.
How do you achieve bearing system optimization through simulations?
The only way wind turbines can achieve maximum operational reliability and cost effectiveness is if they are optimally designed in the first place. Our closed-loop engineering approach uses calculation and simulation programs to provide the basis for optimal design. This involves specialized multi-body simulation programs that generate highly realistic dynamic models of individual rolling bearings, adjacent structures, and even whole drive trains. We are now also exploring machine learning tools and how they can help us use field measurement data in our models. In this context, cloud computing enables us to rapidly analyze large datasets so that we can optimize the mechanics and dynamics of wind turbine bearings.
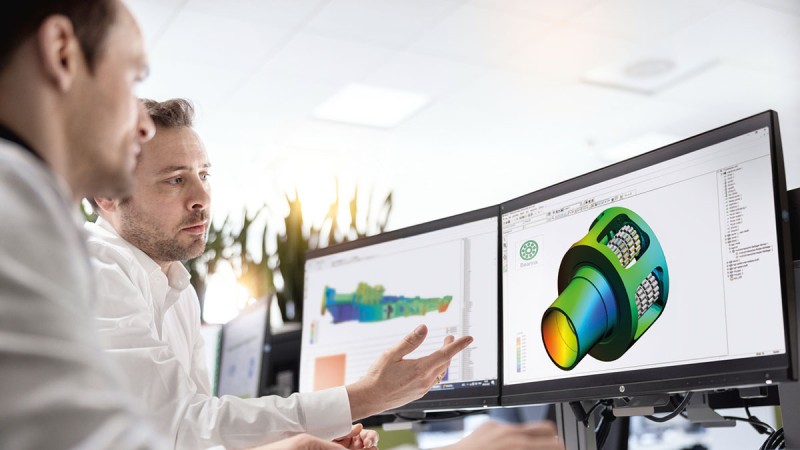
Can these types of bearings really be tested under realistic conditions? How and where do you do this?
Wind turbines operate under permanently changing wind conditions. Our ASTRAIOS test bench for large-size bearings can simulate precisely these kinds of changing conditions – anything from a gentle breeze to a roaring gale. It’s still one of the largest and most powerful test benches in the world. We’ve been using this facility since 2011, and it can test bearings with weights of up to 15 tons and external diameters of as much as 3.5 meters. These types of test bench facilities and the insights they yield are important for the development of new products, which is why we are progressively expanding our testing capacity. For example, the world’s most powerful test facility for wind turbine main bearings is currently being built in Lindø, Denmark, in cooperation with LORC (Lindø Offshore Renewables Center) and R&D Test Systems. Starting in late 2025, we will test our rotor bearings there in cooperation with turbine manufacturers and successively validate our confidence interval with regard to bearing fundamentals and calculation and simulation models for the next generation of wind turbines.
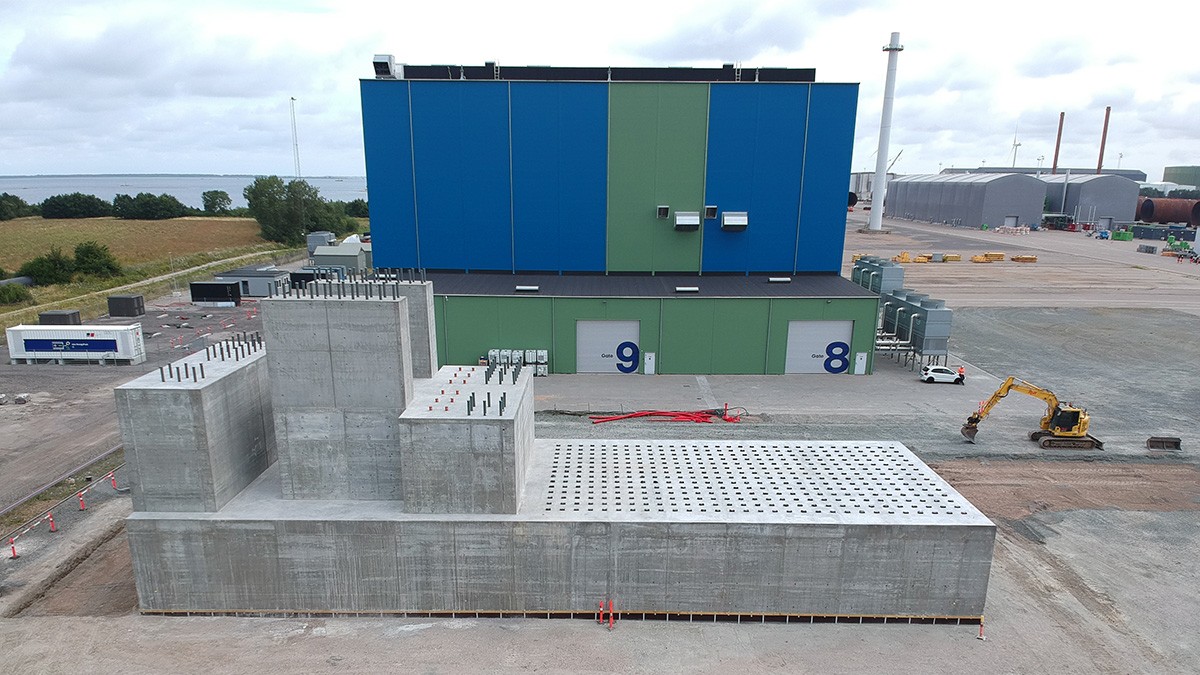
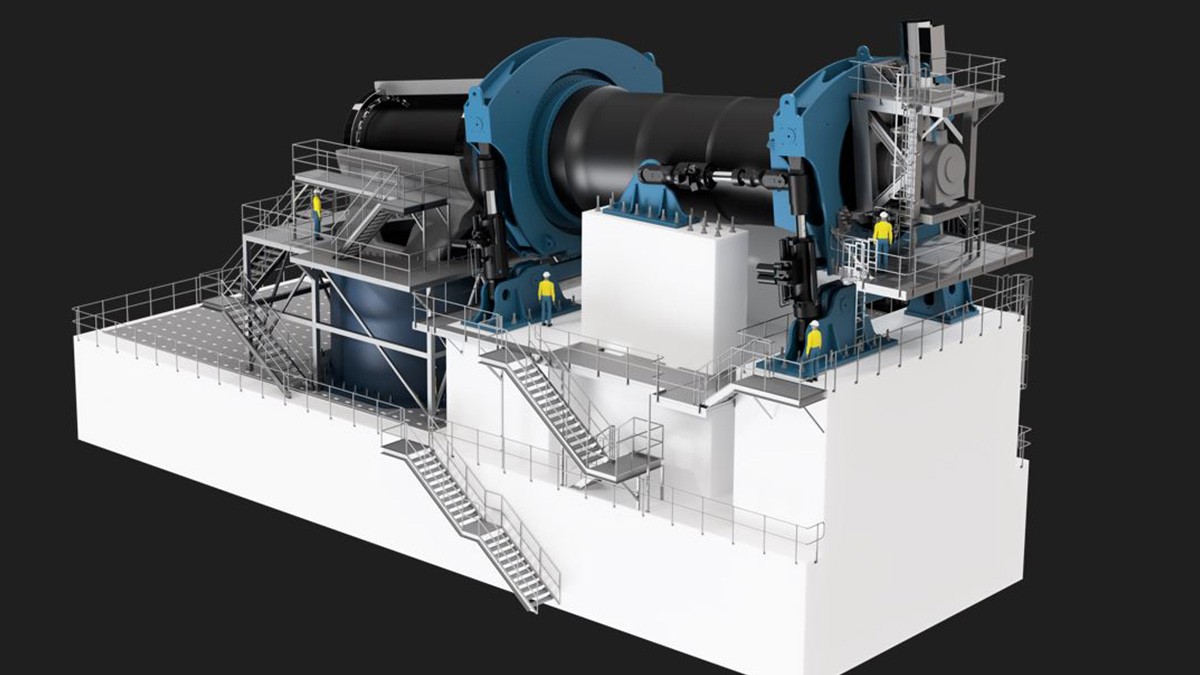
Where do you think the market is heading?
The main focus will continue to be on maximizing wind turbine output and reliability and optimizing energy generation costs over the turbine’s entire service life. With that having been said, there have been some major developments in the market in recent years. The transition to more sustainable forms of energy is an all-encompassing project that is taking the market to a whole new level. The wind farm currently being built in the North Sea is a prime example of this. It will be Germany’s biggest offshore wind farm. Schaeffler’s contribution here is not limited to components. In fact, thanks to our profound systems know-how, we have been involved in this mammoth project as strategic partner right from the development phase. So, it’s all about taking an integrated approach to maximizing wind-turbine reliability and cost-effectiveness. That’s what will be driving the market in the years to come.
Does that mean there will be even greater cooperation between all partners involved in the development process?
Absolutely. The only way we can meet the steadily increasing performance requirements and cost pressures is if we grow our expertise by sharing it with each other. And that means partnership between manufacturers of components, turbines and gearboxes. Ultimately, this benefits the industry as a whole – as you can see from our cooperation with experienced partners like LORC. Without this cooperation, it would not be possible to build the state-of-the-art testing facilities needed for the technological development and optimization of multi-megawatt wind turbines.
Why is wind energy so important to you personally?
Generating energy from wind makes sense because wind, unlike conventional energy sources, offers virtually unlimited availability. What’s more, wind energy is one of the most efficient forms of energy production. A wind turbine will recoup all the energy used for its entire production in the space of just a few months of operation. That says it all, really. At the same time, global demand for energy will continue to rise. Our goal is to help meet this high demand in two ways. The first is by working with our cooperation partners and customers to further increase the efficiency of wind energy. The second is by leveraging our closed-loop engineering approach and high-performance components to ensure that wind turbines are cost-effective to operate.