Green production: A major strand of Schaeffler’s Climate Action Plan
Schaeffler is conscious of its responsibility towards the environment. The motion technology company has therefore developed an ambitious Climate Action Plan to achieve its climate goal and implement the necessary climate protection measures. The plan is based on the Sustainability Roadmap adopted in 2019 and the holistic sustainability strategy that Schaeffler is constantly refining. One of the key focus areas is green production. This is based above all on the decarbonization of production, i.e., reducing greenhouse gas-related emissions in manufacturing processes. An important aspect in the context of resource efficiency is to save water.
Petru-Cătălin Scafaru, Head of Schaeffler Production System and Production Technology, leads a team responsible for the global implementation of measures for green production.
Decarbonization
To achieve the goals of its sustainability strategy, Schaeffler has identified emissions categorized into specific Scopes in accordance with the GHG Protocol Corporate Standard:
- Scope 1 – Emissions released due to the use of fossil fuels in operation.
- Scope 2 – Indirect CO2 emissions, caused e.g. by energy suppliers as a result of purchased electricity or district heating.
From 2023 onwards, these areas are set to be climate neutral as a result of green production measures. The company is striving to prevent 75 percent of production emissions by as early as 2025.
To eliminate emissions, Schaeffler is focusing primarily on improving energy efficiency, using renewable energies, and defossilizing its production facilities. Specifically, this means:
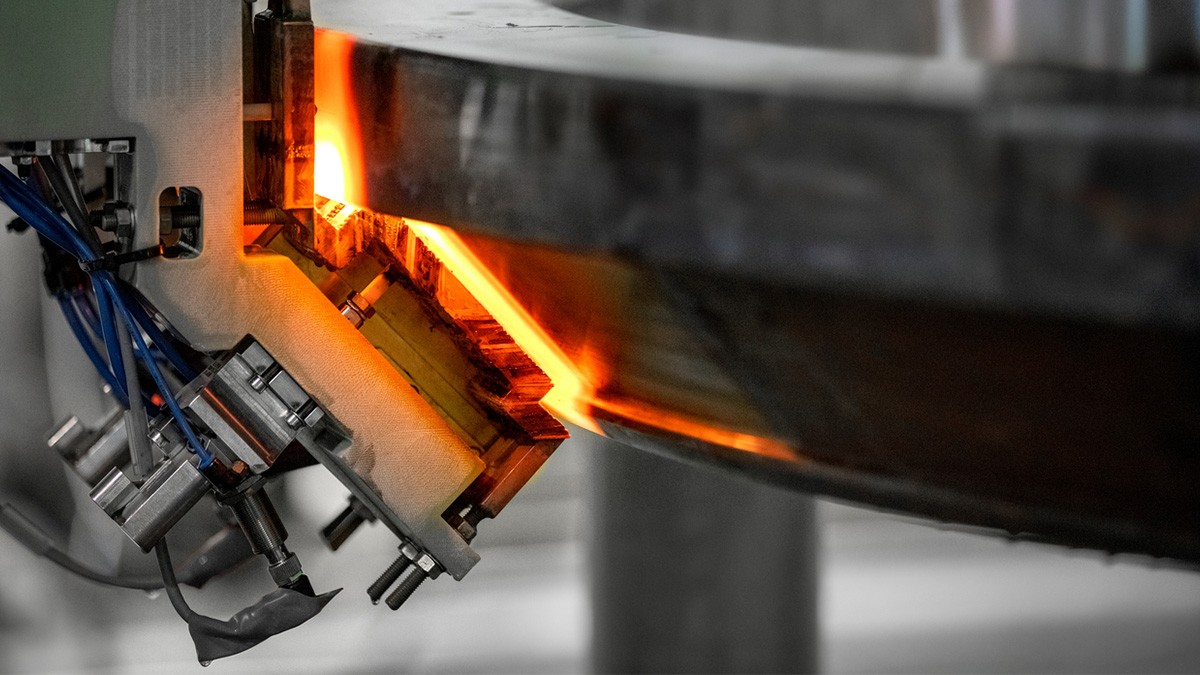
Energy efficiency at our production sites is to increase. Our binding savings target is 100 gigawatt hours by the end of 2024. When it comes to infrastructure, solutions for the heating of buildings, such as heat recovery using heat pumps, help achieve green production. These heat pumps can be used in new or existing buildings. Waste heat from production can also be used for heating. In the area of heat treatment, induction hardening is replacing the more energy-intensive processes previously used.
Schaeffler is aiming to increase the amount of green electricity generated in-house. Since 2022, all of Schaeffler’s European and Chinese plants have been procuring all their electricity from regenerative sources. The company’s plants in North, Central and South America are set to follow in 2023, and the Asia/Pacific region in 2024.
Photovoltaic systems are already being used on our buildings at many locations. The program kicked off in 2018 with PV systems at locations like Pune in India and the logistics center in Kitzingen, both of which are producing 750 kWp. Other systems went into operation in 2021 in Savli, India (270 kWp) and Szombathely, Hungary (55 kWp). Our focus is on on-site and near-site systems – i.e., right on the company grounds or in the vicinity with direct cable connections to our plants. But larger offsite facilities are also included, e.g., the solar power system in Kammerstein that Schaeffler acquired at the end of last year and which in the first six months of 2023 alone produced more than 5 GWh of green electricity.
In addition, Schaeffler is switching from natural gas to alternative energy sources in its production facilities. The defossilization of production facilities is achieved by means of a “fuel switch” to electricity or hydrogen. At three sites, we are currently conducting pilot projects to analyze the use of furnaces that run on hydrogen. In the case of process gases, the switch is to synthetic variants.
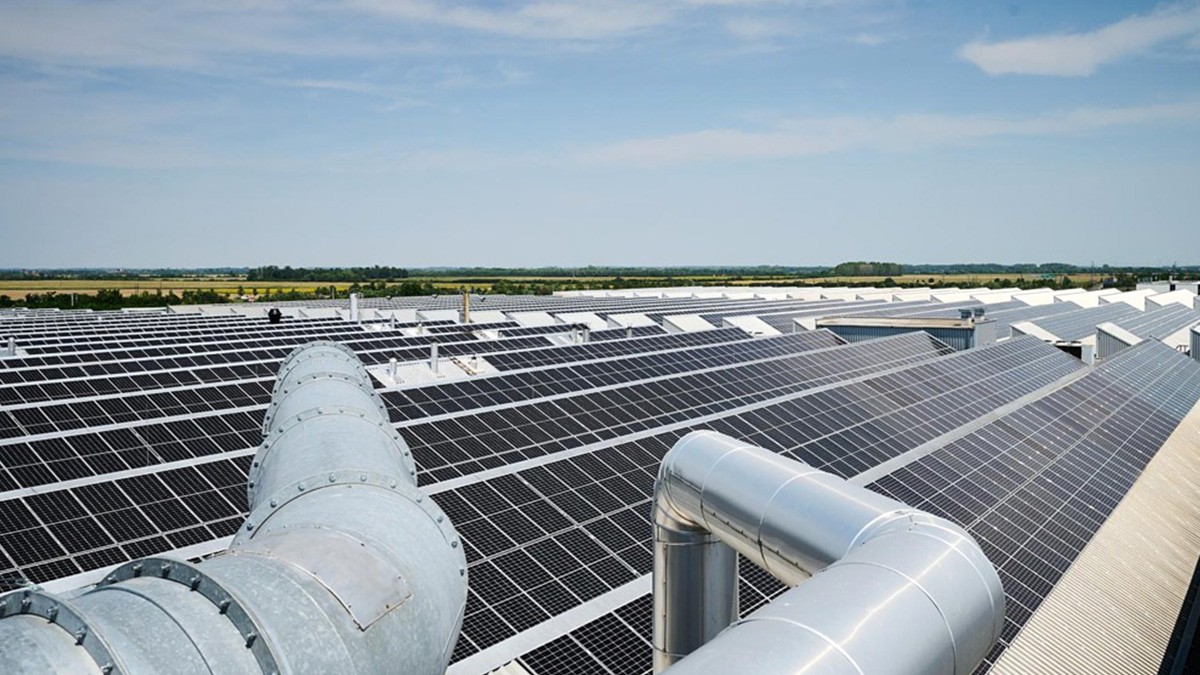
Water savings
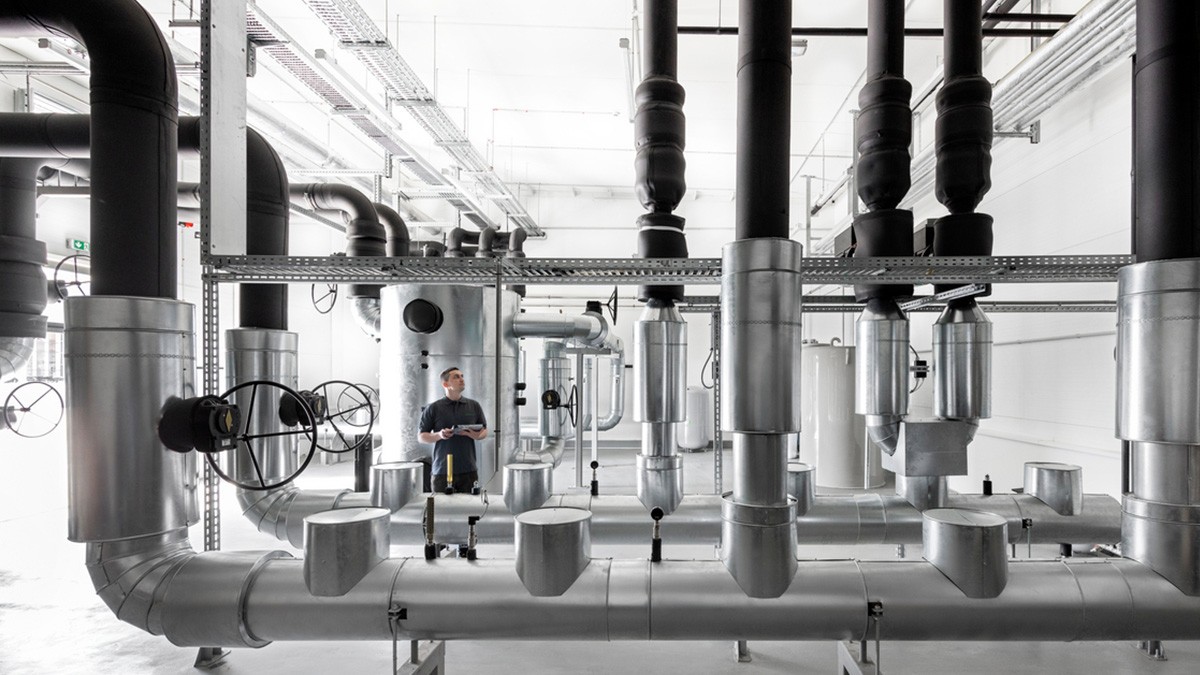
Schaeffler is well aware of the immense importance of water as a resource, today and in the future. The company has set itself the target of of reducing its fresh water abstraction by 20 percent compared with 2019 levels by 2030 – including through green production. Three examples:
During needle fabrication in Elgoibar, Spain, large quantities of water are required in the polishing and tumbling area. This was the reason for installing new, multi-stage wastewater technology with a recirculation system in 2022. The wastewater undergoes chemical and physical pretreatment and is then filtered using membrane technology (ultra-filtration, nano-filtration, osmosis, and evaporator). Currently, about 75 percent of the water can be re-used. Following completion of the optimization measures, this should reach almost 100 percent.
At our French site in Haguenau, a vacuum evaporator system reduces the volume of liquid waste containing oil (e.g. used processing emulsions and oily scrubbing slurry) occurring in the production process. The machine splits the oily waste or wastewater into two fractions in an energy-efficient process. This results in a distillate, i.e., water, which accounts for around 95 percent of the volume introduced. This water can be re-used in secondary processes or discharged to the sewage system in accordance with regulations. The remaining five percent form a concentrate of oily residues that can be recycled. This avoids the need to transport the wastewater to an outside treatment plant and recovers heat from the processes with which the wastewater to be distilled is preheated. As a result, this system reduces both energy and water consumption.
By analyzing the use of water in needle fabrication at our plant in Nanjing, China, it was possible to improve the complex, multi-stage process for wastewater treatment. As a result, the plant in Nanjing is saving 21,000 tons of water per year and producing less special waste. These steps in the management of resource efficiency and environmental protection support Schaeffler’s global target of reducing fresh water abstraction by 20 percent (relative to 2019) by 2030 by means of green production.
More sustainability thanks to employee initiatives
Schaeffler also leverages the knowhow and initiative of its employees worldwide to advance green production. Via the “idea factory” platform, employees can suggest improvements, from which Schaeffler chooses the most promising every year to receive a “best idea” award. In 2022, these included the suggestion for saving water at the Chinese plant in Nanjing, which had come from a team of five colleagues. Another idea from Nanjing was also an award-winner: the optimization of standardized wood packaging for wind turbine bearings. By reducing the number of support beams, dispensing with internal side reinforcements and reducing the internal height and weight of the packaging, more than 240 tons of wood and more than 28 tons of CO2 can be saved every year.
Dezember 2023