Green products – for the environment and the success of the company
The transformation of mobility towards climate-friendly drives is also reflected in Schaeffler’s product portfolio. Green products are found in many areas, from vehicles to machinery and wind turbines. They benefit people and the environment but also secure competitive advantages. This is why CO2-efficient drives play an important role in Schaeffler’s automotive business.
Alongside conventional solutions for combustion engines, there is an increasing focus on hybrid solutions and fully electric drive systems. Schaeffler develops and produces various components and system solutions for the electromobility segment, and in doing so is making a major contribution to the decarbonization of vehicles. Moreover, thanks to its innovative repair solutions, Schaeffler is also doing its part to extend the life of vehicles. For example, Schaeffler has just developed the first repair solution for electric axles.
Over and beyond the automotive sector, Schaeffler is also a trailblazer when it comes to cutting-edge technologies, supplying products and solutions for the industry of the future. The product portfolio of the Industrial division ranges from miniature bearings just a few millimeters wide to large bearings with outside diameters of several meters. The company’s wind turbine bearings have proven effective for decades. Meanwhile, more than a million such bearings have been produced to the Schaeffler Wind Power Standard.
Innovations for electromobility
Schaeffler established its E-Mobility business division in 2018. In 2022, the motion technology company acquired series production projects for the e-mobility segment to the value of €5 billion. Since 2018, the total order value in this segment alone has amounted to €16 billion. It comprises the entire spectrum of electrical drives – for e-bikes, commercial vehicles, and sports cars. They include asynchronous machines, permanent magnet synchronous machines, axial flux motors and magnet-free electric motors known as separately excited synchronous machines.
Current examples of developments in these kinds of green products
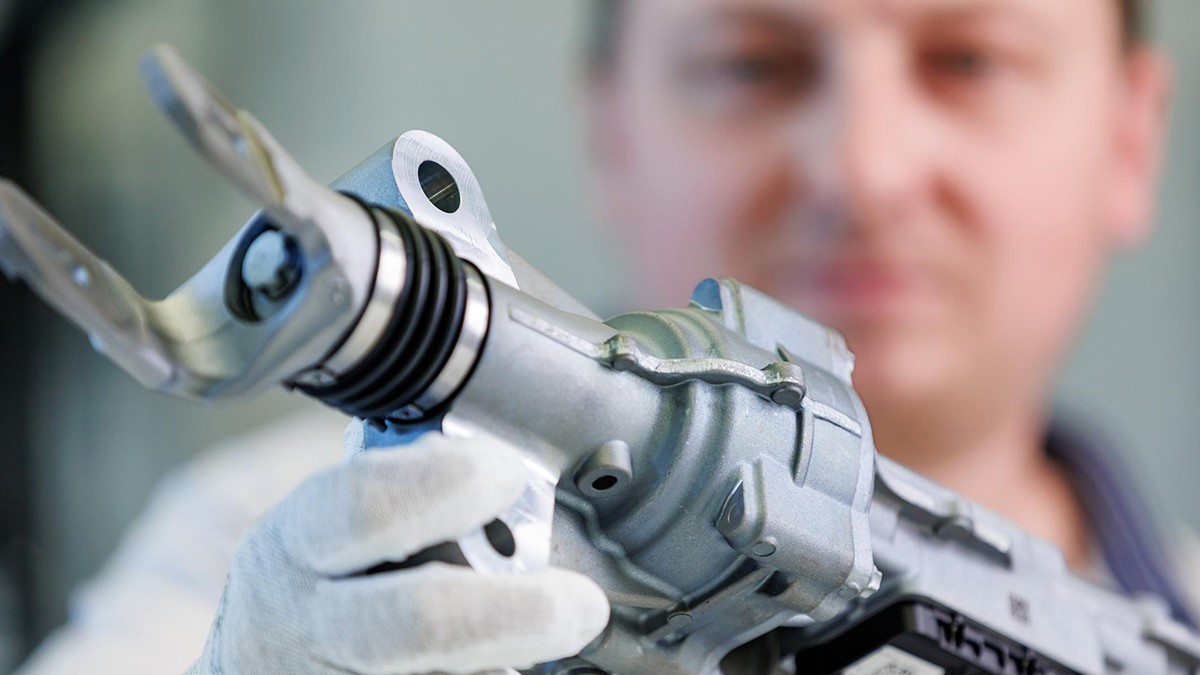
An innovative mechatronic rear axle steering system for E-SUVs which gives vehicles better handling in inner-city traffic, more stability when changing lanes, and maneuverability when parking. The steering system consists of two sub-assemblies – a precision mechanical system with a planetary screw drive, and a power pack comprising the electronics, electric motor, and software. The globally unique planetary screw drive is a further development from the Schaeffler Industrial division. Compared with the trapezoidal screw drives often used in rear-wheel steering systems, this technology meets stringent automobile safety requirements (Automotive Safety Integrity Level, ASIL level D) while at the same time offering much higher efficiency, reduced friction, and shorter system response time. This ensures precise and safe movement of the vehicle.
A 4in1 electric axle with integrated thermal management solution that combines motor, transmission, power electronics and thermal management in a single, optimized unit. The 4in1 electric axle eliminates the additional hoses and cables required by decentralized thermal management systems, so less energy is lost. Fewer parts also means less weight and easier assembly. The integrated thermal management system results in increased range and faster charging time, because it keeps the powertrain, including the battery, at the ideal temperature. Thanks to the interplay between the four sub-assemblies, the 4in1 electric axle can save a compact electric car with a 75-kWh battery about 1 kWh of power per 100 kilometers of travel. That’s approximately seven percent more range, or about 36 kilometers.
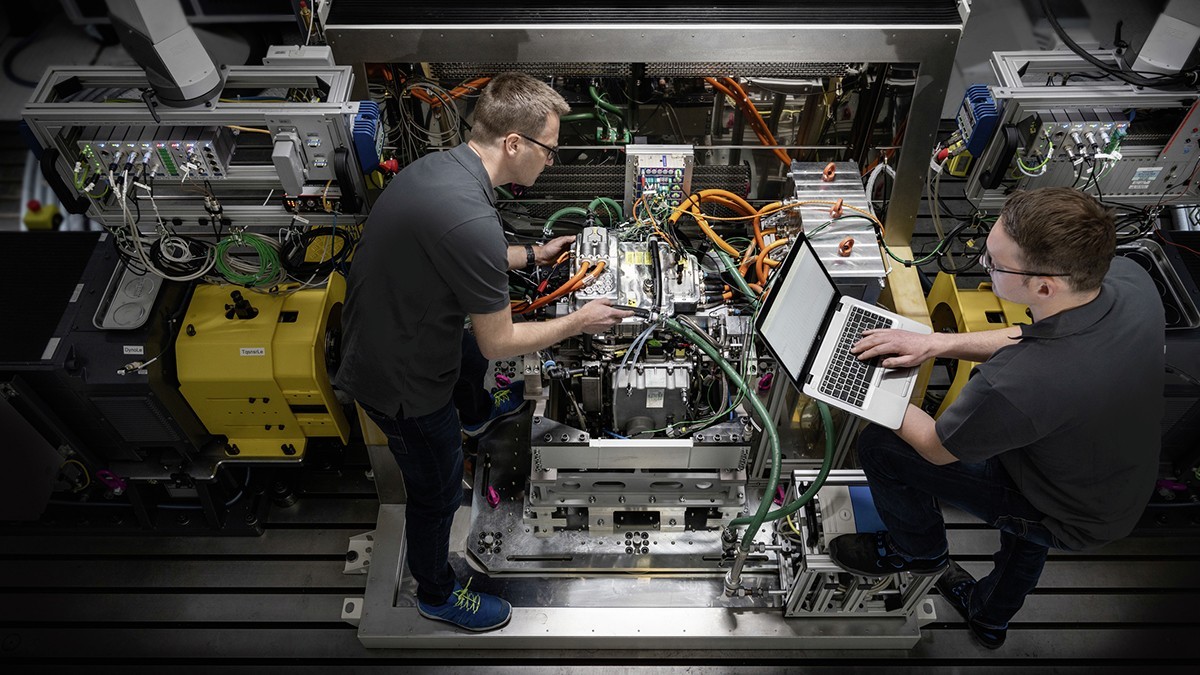
Fully electric wheel-hub drives for municipal vehicles like road sweepers, small vans and snow plows. What’s special about this system is that all the necessary components for drive and brake are installed directly inside the wheel rim. The space saved means that vehicles equipped with this system are smaller and therefore much more nimble and easier to maneuver in inner-city traffic. The low-noise, fully electric drive units ensure that work in pedestrian zones, city streets and residential areas can be done quietly and for longer periods because there is much less disturbance to residents.
The Free Drive chainless drive system for e-cargo bikes: It consists of a pedal generator, drive motor, customer-specific battery solutions, and human-machine interface (HMI) and dispenses with mechanical drive components like chain, sprockets, pinion or belt. The pedal generator produces constant pedal resistance and provides electricity for an electric motor in the rear wheel hub. Surplus electrical energy is stored in the bike’s battery for later use if required. In this way, the Free Drive can deliver a total drive output of 250 watts.
This diverse range of applications and products underscores the fact that there is no single electric motor for vehicles. This is why, when developing these kinds of green products, Schaeffler uses a modular principle in which drives are designed hand in hand with volume production. The company’s investment in the establishment and expansion of manufacturing capacities for electric motors will amount to more than €500 million by 2026.
Components to proven quality standard for wind turbines
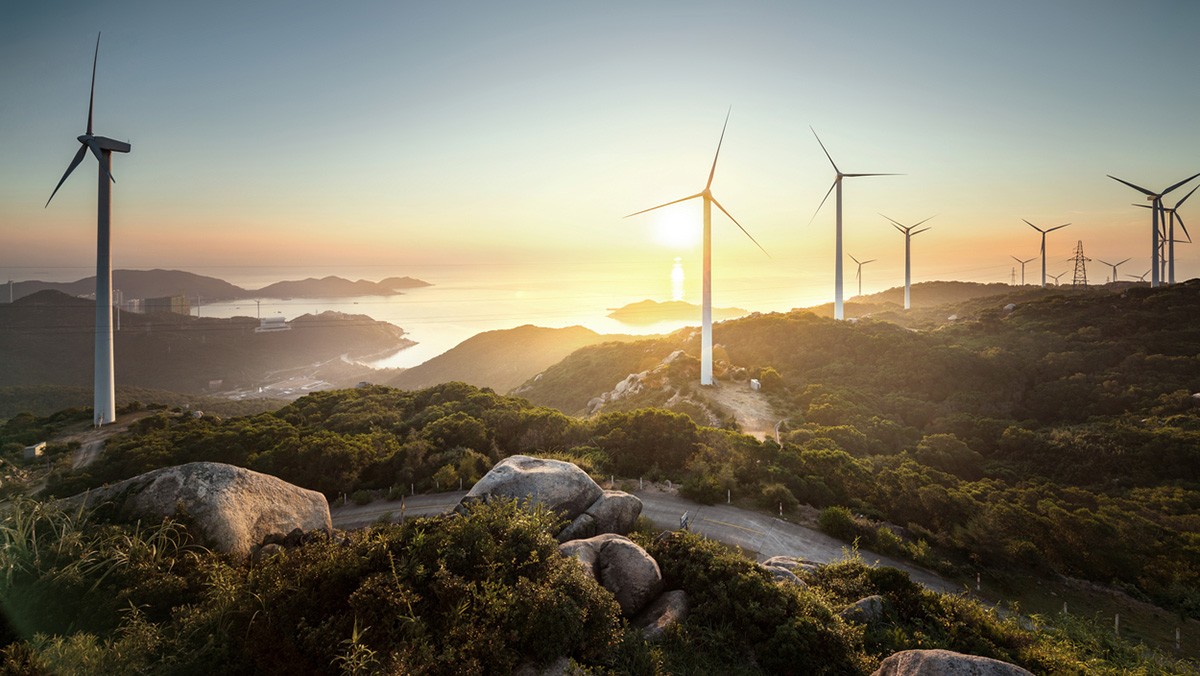
Apart from its activities in the automotive segment, Schaeffler’s focus on green products has long since included components for energy generation using wind power. This form of regenerative energy recovery is a key technology for the energy transition. As a market leader and strategic development partner, Schaeffler has been supplying reliable bearing solutions for onshore and offshore wind turbines for over 40 years. Rolling bearings from Schaeffler are found in every second to third wind turbine worldwide.
As far back as 2012, the motion technology company introduced its Wind Power Standard to ensure the strictest quality benchmarks for these bearings – similar to the kinds of standards that are usual, for example, in the automotive or aerospace industries. The start of 2023 saw the manufacture and delivery of the millionth bearing by Schaeffler in accordance with the Wind Power Standard.
The Wind Power Standard ensures coordinated and transparent processes across the entire process chain in close cooperation with customers and suppliers. These processes include a defined change management structure, a strict quality monitoring system and comprehensive documentation. In this context, a targeted supplier development program ensures the highest level of quality from the very outset – for example in the quality of the steel used due to special material specifications.
The quality assurance process takes place in part on one of the largest, most modern and efficient large bearing test rigs in the world: ASTRAIOS in Schweinfurt. In this facility, bearings weighing up to 15 metric tons and with outside diameters of up to 3.5 meters can be tested by simulating the real-life loads and torques that occur in a wind turbine.
Green products are part of the Climate Action Plan that Schaeffler developed in 2022, because climate neutrality plays a key role in the company’s sustainability strategy.
December 2023