Funded Projects
Our employees at more than 34 R&D centers around the world develop new products, technologies, processes, and methods for solutions that are tailored to the market. Some of the numerous research projects are supported with national and European funding. The research results achieved in the funded projects form the basis for further R&D activities.
Develop a technology for the sustainable electrochemical production of formaldehyde from CO₂ and water
The project "DIAMOND - Boron-doped diamond electrodes for the paired electrosynthesis of sustainable platform chemicals" started on April 1, 2024. The kickoff meeting took place in Herzogenaurach at Schaeffler.
The chemical industry faces the challenge of replacing fossil energies and resources with renewable energies and sustainable carbon raw materials such as CO2 and biomass in the future, while at the same time maintaining security of supply for chemicals and materials. The DIAMOND project therefore aims to develop a technology for the sustainable electrochemical production of formaldehyde from CO2 and water. Formaldehyde is an important platform chemical that has so far been produced by selective catalytic oxidation of methanol.
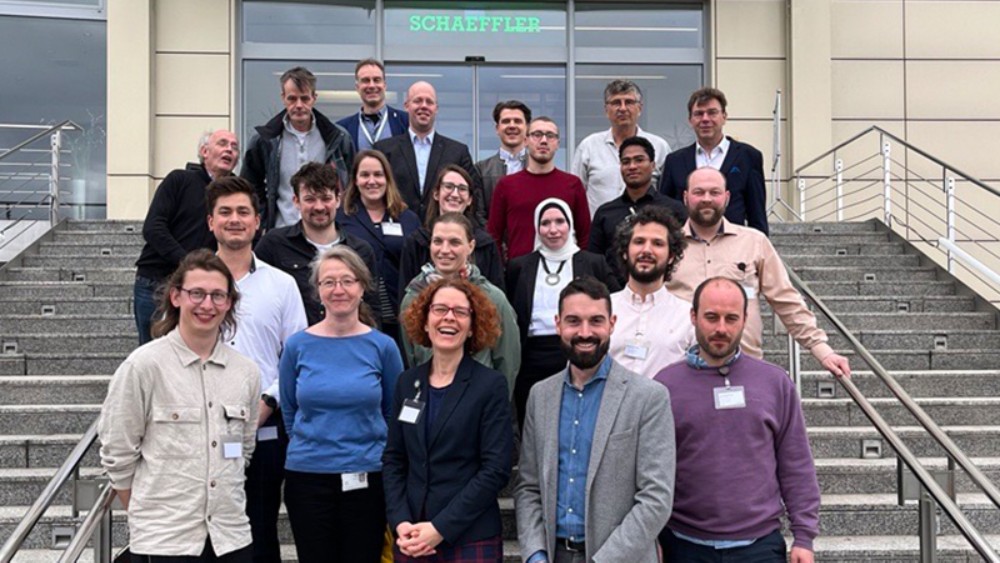
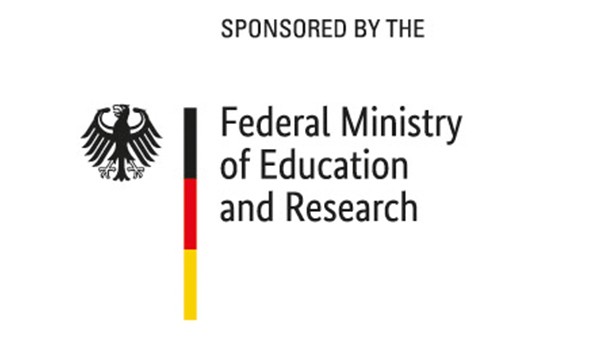
In order to realize the electrochemical conversion of CO2 to formaldehyde economically and on an industrial scale, cathodes and anodes made of commonly available elements are required that are both long-lived and selective for the desired electrochemical conversions in order to minimize efficiency losses. In addition, products with high value-added potential must be generated at the anode. DIAMOND aims to achieve this through the oxidative valorization of bio-based acids.
DIAMOND brings together a highly qualified consortium of partners in the Netherlands and Germany, consisting of academic institutions (RWTH Aachen University, FAU Erlangen-Nuremberg, Fraunhofer Institute for Wind Energy Systems, University of Twente, University of Groningen), technology providers (DiaCCon, Schaeffler) and end users of the technology (Shell). DIAMOND is funded by the German Federal Ministry of Education and Research (BMBF) and the Dutch Research Council NWO with €1.9 million for 4 years.
New manufacturing approaches for hydrogen electrolysers
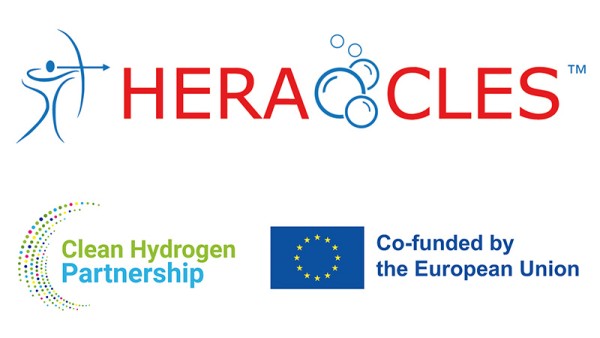
HERAQCLES: Hydrogen Electrolysers to provide Reliable AEM technology-based solutions while achieving Quality, Circularity, low LCOH, high Efficiency and Scalability.
Reducing bearing damage in the drive train of wind turbines
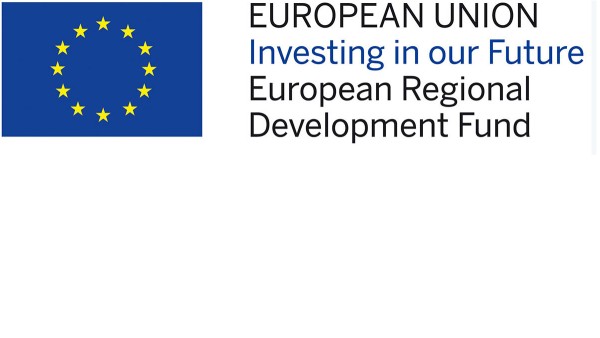
Increasing the reliability of the wind turbines by reducing bearing damage is the main objective of the funding project. The long-term objective is to establish “WEA-Lagerzentrum.NRW”, a wind turbine bearing center in North Rhine-Westphalia.
The cost-effectiveness of power generation from wind energy can be increased by improving the costly repair and maintenance work required as a result of premature rolling bearing damage. As part of the proposed project, two globally unique bearing test rigs will be constructed; one for planetary gear bearings and the other for high-speed shaft bearings in output shafts. The test rigs will approve wind turbine original rolling bearings under realistic operating conditions. The required test rigs are designed to analyze insufficiently explored damage phenomenon.
A list of requirements is currently being created for the development of the test rigs. In the next step, the test rigs will be constructed in the hardware implementation phase and put into operation.
This project will be supported with funding from the European Regional Development Fund (ERDF).